CFD Modeling of a 4-He Evaporation Refrigerator for Polarized Target Experiments
We here present a Computational Fluid Dynamics (CFD) model performed with COMSOL Multiphysics® simulation software as part of a collaboration with the Polarized Target Research Group at the University of New Hampshire (http://nuclear.unh.edu/research/polarized-target-lab/).
By coupling the CFD Module and Heat Transfer Module we solve the 4He (Helium-4) fluid flow of an evaporation refrigerator, predicting its cooling power. This type of cryogenic equipment can reach temperatures down to 1K and it is used in nuclear physics experiments in the process of making spin-polarized samples suitable for electron scattering experiments. Evaporation refrigerators have traditionally been designed using an approximate analytical treatment for the various individual components of the system, which is complex and results in difficulties when attempting to interconnect them and evaluate global behavior. In contrast, COMSOL Multiphysics® allowed us to model the system as a whole and obtain all relevant performance parameters. The main components of a 4He evaporation refrigerator are: radiation shield baffles, precooling heat exchangers, liquid-gas separator, and the “nose” which is the low temperature zone where the near 1K superfluid 4He forms a cooling bath for the target material. Vacuum is provided by a very high-flow capacity Roots-type pump. The geometry, material properties and boundary conditions of all above components of the refrigerator were set in the COMSOL Multiphysics® software. In the modeling, 4He gas is assumed to be a Newtonian and ideal gas fluid. The fluid flow was solved using the incompressible form of the Navier-Stokes equations coupled with the energy-conservation equation. A mesh-independence validation of the modeling was done using the COMSOL Multiphysics® mesh tool. The results obtained were used in the successful construction and operation of a prototype built by the University of New Hampshire. Testing of the completed refrigerator confirmed that the design objectives were met, proving the usefulness of our approach. As an example, we mention that the difference between predicted and empirical cooling power was less than 7.5%, which is considered excellent given the complexity of the system. To the best of our knowledge this is the first time that a CFD analysis has been used in support of the construction and empirical validation of this type of refrigerators. The methodology we used proved to be highly effective and will allow easily adding design improvements, thermal studies and thus achieving a better understanding of all components and their interaction.
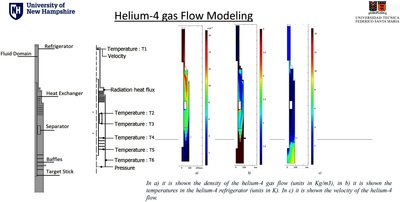
Download
- aliaga_poster.pdf - 1.56MB
- aliaga_cfdfsi_presentation.pdf - 2.34MB