Computational Fluid Dynamic (CFD) Modelling of Methanol Steam Reforming in Microreactors
Microreactors have been used for renewable fuel production due to benefits such as, enhanced mass transfer, improved heat transfer and larger surface-area-to-volume ratios. The steam reforming of methanol over a CuO/ZnO/Al2O3 based catalyst (BASF F3-01) is investigated using 2-D packed bed and coated wall microreactors. CFD methodologies were used to model the transport phenomena and the thermal properties of the gas mixture associated with the composition of each species throughout the reformer. 2-D microreactor models were simulated based on the following assumptions: (a) the concentration and temperature gradients only occur in the axial direction; (b) the methanol-steam mixture flow is taken to be steady state and radially uniform throughout the packed catalyst bed; (c) the ideal gas law is valid for the gas species in the microreactor; (d) the axial fluid velocity is constant with uniform physical properties and transport coefficients. The gas species react heterogeneously with the catalyst. The transport of diluted species physics in porous media interface was utilised to generate the species concentrations and transport in the reacting media. In addition, the Chemical Reaction Engineering Module was applied to simulate the reaction and reacting conditions within the microreactors. The reactive pellet bed feature simulated the particle fluid reaction phenomena occurring within and around the catalyst particle and further allowed the investigation of internal and external mass transfer limitations in the microreactors. The mass balance equations coupled with the appropriate boundary conditions were solved using COMSOL Multiphysics®. The geometry for the packed bed microreactor comprised of a mesh consisting of 568,000 domain elements and 32,265 boundary elements, and 108,254 degrees of freedom was used, the results were found to be mesh independent with a computational time of 7.5 seconds. The geometry for the coated wall microreactor comprised of a mesh consisting of 684,154 domain elements and 56,257 boundary elements, and 120,300 degrees of freedom was used, the results were found to be mesh independent with a computational time of 8 seconds. The CFD microreactor models were compared to experimental data from literature to assess the validity of the results, and a good agreement between the two sets of data were observed. Further parameters such as, the size of catalyst particle and the wall coating thickness were investigated to assess their effects of product composition and methanol conversion. Figure 1 depicts the comparison between the packed bed and coated wall microreactor at a reaction temperature of 210 oC, and varying catalyst particle sizes. The results show that as the temperature increases, the methanol conversion also increases. Furthermore, increasing the catalyst loading (mcat) also enhances the methanol conversion. It can also be observed that there is a small difference in methanol conversion between the 75 µm and 150 µm catalyst particles, and so it appears that there is an insignificant influence of catalyst particle size on conversion. To conclude there is potential for microreactors to increase the fuel production volume by means of scaling up, and their ability to be used for offshore fuel production.
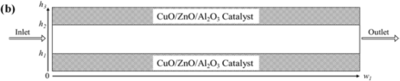
Download
- COMSOL 2020.pptx - 0.74MB