COMSOL® Application to Estimate 3D Blast Furnace Hearth Wear Using Thermocouple Measurements
The blast furnace is a counter flow reactor to produce pig iron. The molten pig iron and byproduct slag are accumulated at the hearth of the furnace, from where they are tapped regularly. The blast furnace has to stay continuously in operation for many years to prevent solidification of molten metal in the hearth except for some short stoppages. The lifespan of the blast furnace is governed by the erosion of the hearth refractory. Once the residual thickness of the refractory lining is critically low, it must be repaired during a long-term stoppage which is quite costly. Therefore, it is essential to keep track of the residual lining thickness not only for the better planning of the relining but also for the operational safety (i.e., avoiding dangerous hearth breakthrough incidents).
Modern blast furnaces are equipped with many thermocouples in the hearth refractory to monitor the temperature level which corresponds to the refractory wear. An inverse 3D heat transfer model has been developed to estimate the 3d hearth wear profile which fits best to the current thermocouple measurements on a daily basis. The LiveLinkTM for MATLAB® has been utilized to interpolate the 3d wear profile from the wear parameters (by using Kriging algorithm) and to optimize (by using the Levenberg–Marquardt algorithm). At each iteration step of the optimization, the COMSOL Multiphysics® model for heat transfer in solids is solved using a different wear profile for the temperatures at the thermocouple positions. The developed model is daily solved using COMSOL ServerTM with MATLAB®. Furthermore, a COMSOL® application has been programmed as a user interface to visualize the results such as residual refractory thickness, temperature contours, historical evolution of wear parameters and temperatures, etc.
The developed model has been calibrated and validated by comparing the estimated wear profile with the measured residual wall thickness during the last relining at Eisenhüttenstadt and Dillinger plants. Currently, the model is being planned to be used at these two plants for monitoring the online hearth wear state. The blast furnace operators can access a variety of model results by just using a web browser. The most useful plots are residual refractory thickness contours plotted on the 3d hearth wear surface or 2d unrolled hearth wall, the temperature contours in a selected vertical or horizontal section through the hearth refractory lining, and the historical evolution of wear parameters and temperatures.
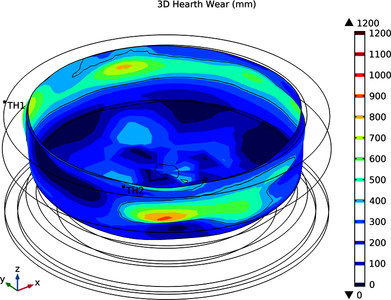
Download
- kaymak_presentation.pdf - 1.17MB
- kaymak_poster.pdf - 1.45MB
- kaymak_paper.pdf - 0.88MB
- kaymak_abstract.pdf - 0.17MB