Finite Element Modelling and Simulation Tools for Investigation of the Process and Materials 3D-Printed by Selective Laser Melting
Selective Laser Melting (SLM), like many other additive manufacturing techniques, offers flexibility in design expected to become a disruption to the manufacturing industry. The current cost of SLM process does not favor a try-and-error way of research; which gives more room for modelling and simulation in that field of research. In this work we present a full model using Finite Elements Methods to solve a multi-scan SLM process problem using COMSOL Multiphysics Software.
In this work, a combination of physics like ray-tracing, heat transfer with phase change, laminar flow, and deforming geometry was used. This is enabled by provision of Ray Optics, Heat transfer and Structure Mechanics or CFD modules. Ray tracing was used to finetune the analytical description of laser absorption during laser interaction with granular or bulk material. The analytical model deduced for laser absorption was used as input in heat transfer model. Laminar flow was coupled to heat transfer to describe mass transfer in the melt pool; mainly due to Marangoni effect, recoil pressure and body forces during laser scanning. To account for geometry reformation during solidification, deformed geometry can be used to estimate the final surface topology from melt pool track traces. COMSOL applications can be built to facilitate users without deep background in modeling and simulation to perform easy parametric study of the process. Long term use of the model has produced enough results for different combinations of parameters to be used for a machine learning model to estimate the process quality for new parameter with very low computation cost.
In the model, a combination of Ray-Tracing technique, a solution of the Radiation Transfer Equation and absorption measurements is used to establish an analytical equation that gives a more accurate approximation of laser energy deposition in powder-substrate configuration. With the new energy deposition model, other physics involved in the process are carefully set as well. The adjusted model is able to produce reliable cooling curves and melt truck geometry that explain well experimental observations. One of the applications is the use of simulated tempering parameter, from Holloman-Jaffe equation, to investigate the martensite inclusion across the printed part and match it with local micro hardness.
References
- H. J. Willy, X. Li, Z. Chen, T. S. Herng, S. Chang, C. Y. A. Ong, C. Li, J. Ding; Model of laser energy absorption adjusted to optical measurements with effective use in finite element simulation of selective laser melting, Materials & Design 2018, 157, 24
- X. Li, H.J. Willy, S. Chang, W. Lu, T.S. Herng, J. Ding, Selective laser melting of stainless steel and alumina composite: experimental and simulation studies on processing parameters, microstructure and mechanical properties, Mater. Des. 145 (2018)
- X. Li; Y. H. Tan; H. J. Willy;Pan Wang; Wanheng Lu; M. Cagirici; Dr. C. Y. A. Ong; Dr. T. S. Herng; Prof. J. Ding, Heterogeneously tempered martensitic high strength steel by selective laser melting and its micro-lattice: Processing, microstructure, superior performance and mechanisms, Mater. Des. (2019)
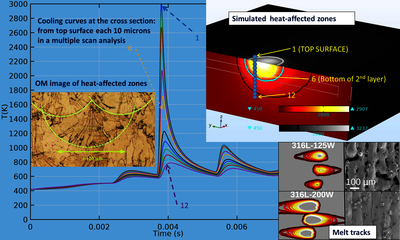
Download
- jean_willy_heatrans_presentation.pdf - 2.62MB
- jean-willy_poster.pdf - 1.86MB