Heat transfer optimization in hybrid manufacturing processes of high performance composites
COMSOL Multiphysics® and LiveLink™ for MATLAB® had been used to perform a thermal optimization of a hybrid manufacturing process. In this work, a thermo-stamping of high-performance thermoplastic composites with a metal insert followed by an overmolding process, has been chosen as an application example. The first process stage consists of the preheating, on an infrared oven, of two high-performance thermoplastics composite blanks and a metal insert between them. The assembly is then transferred into the mold cavity to be stamped before over-molding steps. Finally, the part is cooled down and removed from the mold to let another cycle start. (figure 1).
This study intends to determine the spatial and temporal distribution of the heat sources and sinks that must be applied either on the external surfaces of the assembly or on an enveloping surface created around the part, this enveloped configuration is based on the concept of conformal cooling [1,2]. The choice of the location of the searched heat flux depends on the studied stage (figure 2). The estimated heat flux must satisfy a thermal objective within the part. This objective can be, for instance, the achievement of a temperature level or the absence of temperature gradients, which will correspond to quality / productivity criteria.
Once a 2D axisymmetric model is created the optimization problem is treated as an inverse problem subjected to constraints. Thus, it requires the calculation of the direct problem, the processing of the adjoint state and the development of the sensitivity equations to implement a first-order gradient-based algorithm. All these physics are treated on COMSOL Multiphysics® Heat Transfer Module. The “Heat Transfer in Solids” is used to perform the direct and sensitivity problem at each stage (preheating, transfer, stamping, over-molding and cooling) while a General form PDE is used to solve the adjoint problem also by stage. All of them as a time dependent study. The physics are established by domain (metal insert, composite, polymer and mold zone). Each physics domain has varying boundary conditions in space and time according to the solved study, for which we used interpolation functions. Besides, because all the stages are coupled, we use the final temperature profile of one study as an initial condition to the subsequent study. Once the physics are in place, Matlab Livelink is used to program the optimization loop. The optimization procedure leads to finding the optimal boundary conditions as a time function at each stage of the process.
First results shows a good improvement on top and bottom surfaces temperatures profiles distribution of the final part, reducing temperature gradients at each stage while arriving at the established target temperature. Forward study will take into account maximum and minimum temperature levels and heating/cooling rates as constraints.
- Xiaorong, & Xu. (1999). Conformal Cooling and Rapid Thermal Cycling in Injection Molding With 3D Printed Tools
- Agazzi, A. (2011). Contribution à l’optimisation de la thermique des outillages dans le procédé d’injection des polymères thermoplastiques.
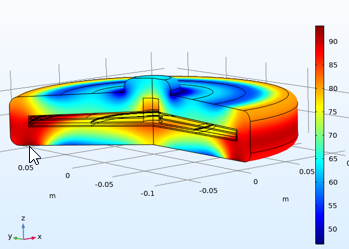
Download
- Presentation_Comsol 2020.pptx - 1.25MB
- Europe_2020_Poster.pptx - 0.57MB