Hybrid 2D/3D fully coupled electrothermal model for three-core submarine armored cables
It is a fact that IEC 60287 standard introduces important errors in the computation of the armor losses of submarine three-core lead sheathed armored cables, since the twisting of phases and armor wires is not considered. This results in an overestimation of cable size, and hence its cost, highlighting the need of an accurate tool that provides the most suitable cable for a safety operation in a particular location, minimizing not only installation cost, but also operational cost. For this task, 3D finite element simulations in COMSOL Multiphysics® have proved to provide accurate results for the computation of three-core armored cables losses, thanks to recent advances that help in reducing the model length by applying rotated periodicity boundary conditions. However, for obtaining the ampacity of a particular cable, a fully coupled electrothermal model is required. Since the cable is composed by many elements and layers, a fully coupled 3D electrothermal model would require a highly detailed 3D geometry, something that can be difficult to be implemented since especial operations are required when building and meshing the geometry for applying periodic boundary conditions. This worsens when analyzing cable filler design, where mesh complexity increases drastically since natural convection and radiation have to be solved inside the gaps (hence higher computational resources would be required also). To overcome this problem, a hybrid 2D/3D fully coupled electrothermal model is proposed in this work (Fig. 1), where the AC/DC module is employed to solve the electromagnetic problem in a simplified 3D geometry (Fig. 2). Then, the computed losses distribution in a particular cross section of the 3D model is employed as the heat source in the Heat Transfer module to solve the thermal problem in a detailed 2D geometry (Fig. 3). The temperature distribution obtained is then sent back to the electromagnetic model to update the electrical resistivity of the materials. All this is done by using General Extrusion operators that must be adequately configured to take into account the helical path of phases and armor wires (Fig. 4). Through this procedure, the temperature distribution of a three-core armored cable can be obtained in less than 10 minutes in a 64 Gb of RAM laptop. This can be further reduced if the 3D model is again shortened up to CP/n thanks to its periodicity, where CP is the so-called crossing pitch and n is any divisor of the number of armor wires. However, this may lead in less accurate results in the computed losses for the shortest model length (higher values for n). Nonetheless, a good balance between speed and accuracy is found for n ranging from 3 to 40 (if any divisor of the number of wires exists). The results for a real cable show that the better characterization of losses provided by the hybrid method leads to an ampacity estimation of about 5 % lower than that derived from 2D. The full work will present a comprehensive comparison for different cables from 115 kV to 220 kV.
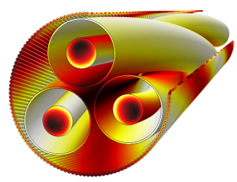