Modeling of the Ladle Furnace Preheating with a Graphite Heating Rod
This work, which is done in the framework of the SisAl Pilot EU project, presents the use of the COMSOL Multiphysics® software for simulating ladle furnace preheating. The SisAl Pilot project aims at optimising the silicon production in Europe by recycling materials and using a carbon-emission friendly technology. The silicon production experiments are conducted on laboratory and pilot scales in different types of furnaces, including ladle furnaces. Besides experimental work, the process optimisation also relies on the numerical modelling. The present model simulates the preheating of an existing ladle furnace with a graphite heating rod used as a resistive element powered by a DC electric current. The aim of the work is to tune unknown problem parameters, especially graphite properties, by fitting experimental temperature curves. The adjusted material properties will be further used in the SisAl Pilot project for the numerical analysis of new ladle furnace designs. In general, the graphite properties, such as density, heat capacity, thermal and electrical conductivity, are functions of temperature and can vary depending on the material type and supplier. In the present study, we assume that the heating rod graphite and the crucible graphite differ from each other only by their porosity. With this assumption, a single set of temperature-dependent graphite properties, found in literature, can be generalised by modulating it with the material’s porosity according to a preferred analytical model (Landauer’s relation in this work). This makes porosity a single tuning parameter for each type of graphite in the model. The experimentally measured electric current through the heating rod serves as a known model input parameter. Measured electric power and temperatures are used for the model tuning and validation. The following COMSOL® physics interfaces are employed in this model: Heat Transfer in Solids and Fluids with convectively enhanced gas conductivity, Surface-to-Surface Radiation, and Electric Currents to simulate the Joule effect in electrically conducting materials. A bidirectional coupling of all the interfaces is present due to multiple interdependencies via material properties. The proposed numerical model has successfully simulated the ladle furnace preheating. The work is validated against experimental data: the tuning of model and material parameters has resulted in a satisfactory fitting of experimental curves. The adjusted graphite properties are ready to be exploited in the next stage of the SisAl Pilot project, which is focussed on the numerical analysis of new furnace designs. The presented approach of tuning material properties can be applied to other problems dealing with porous materials.
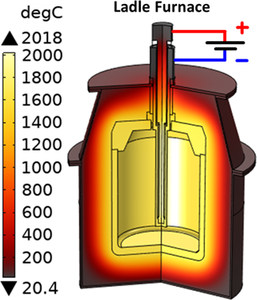