Numerical Prototyping of Locally Heated Digital Microfluidic Devices
An alternative approach to integration of a local heat source with the digital microfluidic (DMF) platform by attaching inkjet-printed silver microheaters to the bottom plate was recently introduced (Sathyanarayanan et al., MNE 2017). This approach allows more degrees of freedom to the chip design, since the microheater can be redesigned on demand and placed anywhere below the bottom plate (Fig. 1a), without occupying the actuation electrodes at the heated position. Here, we report a numerical study to analyze the resulting temperature gradients within both the heated digital microfluidic (DMF) chip itself and within the heated (aqueous) droplet. Time dependent heat transfer equation which consists of heat source, heat storage and heat transfer in three dimensions is solved by heat transfer module of COMSOL Multiphysics®. The finite element (FE) mesh of the domain was generated using tetrahedral elements and swept mesh along the vertical direction within the thin layers. The mesh size was refined in the proximity of the heater where higher temperature gradients are expected. A mesh independency analysis was performed and an optimum element number (38802) was chosen to reach a converged result. In order to decrease the mesh numbers and solution time, thin layer approach was used to model the chromium electrodes, the fluoropolymer layer, and the thin oxide layer. Numerical results were verified against temperature measurements of the top surface of the DMF chip. In both numerical and experimental study, the aqueous droplet was encapsulated in octanol as illustrated in the Fig. 1a so that evaporation effects could be omitted. In this manner, the measured temperature values showed good match with the simulation results. Validated COMSOL model was used to study how the heated location will affect the temperature gradients. Four different heater locations were studied providing temperature value of 37 °C within the aqueous droplet. Required power values for each heater to reach this temperature were determined. It was shown that temperature gradients are small enough in vertical and horizontal direction allowing uniform heating of the aqueous droplet with all four different heater locations (Fig. 1b-d).
Reference: Sathyanarayanan, G., Haapala, M., Sikanen, T., “Digital microfluidic enzyme reactor with integrated low-cost printed microheater”, The 43rd International Conference on Micro and Nanoengineering (MNE) 2017, Braga, Portugal, September 18-22.
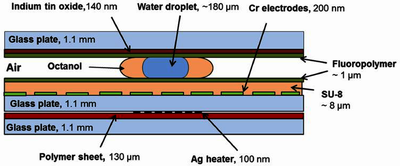
Download
- Özen_poster.pdf - 0.04MB
- Özen_abstract.pdf - 0.34MB