Simulation of Mixing and Polymerization in 3D-Printed Tubular Reactors including SMX-Mixing Elements
The progress within the field of additive manufacturing has eased the fabrication of new reactor geometries significantly. It is possible to design and print a reactor of tailored shape and size at comparatively low costs and short time. Printing and testing all sensible reactor designs will counteract the promise of a fast development and short time to market. To reduce the needed number of printed models, one approach is simulating and optimizing the mixing of solutions and the influx of reactive heat with CFD before printing. This indeed then allows for significant reduction of development time and thus costs. For chemical reactions which are highly sensitive to fluctuations in concentration and temperature such as radical polymerizations, part of an optimization is the evaluation of mixing components and reactive heat dissipation in the reactor. Within the work present here, the degree of segregation in a range of tubular reactors containing SMX-type mixing elements was simulated and optimized with respect to total reactor volume and efficiency of mixing. In a second step, the polymerization of n-butyl acrylate was simulated in the reactor geometry by a method of moments approach. The geometry of the reactor was setup within COMSOL Multiphysics®. This allowed for the variation of height, angle and number of the mixing elements within a parametric sweep. Stationary flow and pressure fields for the reactors were computed for viscosities between 0.001-100 Pa∙s, using the Laminar Flow interface, as the inlet velocities yielded Reynolds numbers below 100. After obtaining the flow field, a Transport of Diluted Species interface was used to obtain the stationary distribution of a tracer, originating from an unmixed inlet, throughout the reactor. The Degree of Segregation within the flow was evaluated via Boundary Probes placed on either side of the mixing elements. As reaction of interest, the polymerization of n-butyl acrylate was simulated in the reactor by including up to the second moment of radicals and polymer as species with according reaction rates in a Transport of Diluted Species interface. This approach was validated by comparison to an existing kinetic model (within Predici™). The heat of polymerization was included via a Heat Transfer in Fluids interface. The simulations show a more even distribution of temperature and polymerization reaction rate within the reactor as opposed to an unmixed tubular reactor. The finalized reactor geometry was exported and printed out of polypropylene filament.
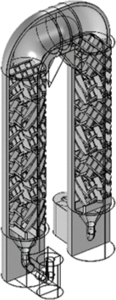
Download
- Poster_Hapke_Conference.pptx - 0.48MB