Understanding the increased performance of novel interconnected-channel monolithic reactors
The versatility of the 3D printing technology has allowed developing originally structured catalysts for interesting reactions, for instance, the 0.5wt.%Fe/SiC monoliths for the treatment of industrial wastewater. These monolithic structures, manufactured by Robocasting, have interconnected channels according to distance of ∼1.3 mm between the filaments in the linear array of their computer-aided design [1].
The millimeter dimensions of the monoliths make it very difficult to experimentally conduct a fluid dynamics study to understand the flow behavior inside the channels and ultimately, how this novel design, affects the reactor performance. The purpose of this study is to compare the classic honeycomb monoliths with squared cells (referred as M) to the 3D monoliths with interconnected channels and triangular cells (3D-M). The oxidation of volatile organic compounds (VOCs) has been considered as target reaction.
The geometry and the dimensions of one channel of each monolith are provided in Figure 1.
Simulations were accomplished using the CFD Module of COMSOL Multiphysics®. To select the appropriate module to carry out the simulation, the operating conditions for the reaction performance were first considered: QG= 120 mL min-1, T= 423K and P= 1atm. Taking into account the monoliths dimensions, the Reynolds number is lower than 100 therefore, a Laminar Flow Module. Besides, Particle Tracing for Fluid Flow Module has been used to study the flow inside three interconnected channels in 3D-M configuration.
The simulation results show that linear velocity of the gas at the entrance of the channel drastically increases, being this value higher for the 3D-M (0.03 m/s) than M (0.02 m/s), due to the smaller size of the 3D-M hydraulic diameter (Figure 1). The linear velocity remains constant along the channel due to the short residence time of the gas into the monolith (around 1 s for 3D-M and 2 s for M).
The radial velocity profiles in Figure 2 show that the gas molecules in the interconnections of the 3D-M monoliths are in movement, though the velocity is one order of magnitude low that in the center of the channel. Thus, some gas flow likely occurs between consecutive channels. In fact, the flow study inside three channels interconnected confirms that the gas passes through two consecutive channels (around 43% of inlet flow pass through one channel to another). The gas trajectory can be visualized in Figure 2. It is possible to observe the impact of the gas molecules against the walls, which is responsible for the helical trajectory of the gas along the channel.
In conclusion, the design configuration of the triangular channel system in which the interconnections are alternately confronted leads to a helical trajectory, which enhances the turbulence and therefore the reactant contact with the catalytic walls. Thus, it is expected that this 3D design of the catalyst has a positive effect on the reaction performance of the monoliths, a study that is now in progress.
References [1] A. Quintanilla et al. 3D-Printed Fe-doped silicon carbide monolithic catalysts for wet peroxide oxidation processes. Applied Catalysis B: Environmental, 2018. 235: p. 246-255
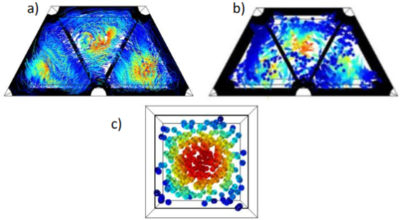