Analysis of Micromixers to Minimize Scaling Effects on Reverse Osmosis Membranes
Abstract
The standard diamond-shaped mesh spacers commonly used in spiral wound membrane elements results in non-ideal hydrodynamics that can lead to fouling, which ultimately reduces the flux of water through the membrane and the operational life of the unit. To address this shortcoming, a novel method for separating RO membrane leaves in spiral wound elements was developed and evaluated. Three-dimensional (3-D) printing was utilized to manufacture micromixers directly on membrane swatches. To enhance performance, a two-dimensional computational fluid dynamic model was used to select the optimal geometry and pattern of 3-D printed micromixers. The optimal geometry selected created unhindered flow between 0.2 m/s and 0.3m/s, using an inlet flow velocity of 0.104 m/s, across 40% of the membrane surface. Laboratory experiments were conducted to evaluate the performance of micromixers and compared to unmodified membranes with a standard 20 mil (0.508 mm) mesh feed spacer. Pure water flux and salt rejection were found to be similar to standard membranes, indicating the 3-D printing process did not damage intrinsic membrane properties. Calcium sulfate scaling experiments were conducted. Scale initially began to form within 2 hours of treatment resulting in a flux decline ofapproximately 10% for both modified and unmodified membranes. Over 14 hours, an average flux decrease of 24% was observed for modified membranes compared to an average flux decrease of 78% for the unmodified membranes. This demonstrated the improved resistance to fouling created by the open channel design with optimal flow conditions. Micromixers printed directly to the membrane surface offers the ability to optimize feed channel hydrodynamics, reduce scale formation and minimize flux decline representing a significant advancement in membrane technology.
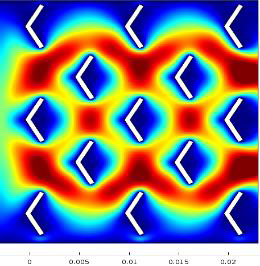
Download
- walker_cfdtransport_presentation.pdf - 0.98MB