Mixing Considerations in Chemical Reactor Scale-Up
The yield and selectivity of a chemical reactor are controlled by the rates of desired reactions relative to those of undesired side reactions. These reaction rates are controlled by the local concentration of reactants, as often described by elementary rate laws. Chemical engineers control these concentrations by manipulating the mixing properties within a reactor, thereby designing a system with optimal product composition. The effect of mixing on the yield and selectivity of a chemical reactor is often demonstrated by comparing two idealized reactor models; the continuously stirred tank reactor (CSTR) and the plug flow reactor (PFR), which approximate complete (i.e. perfect) mixing and zero mixing, respectively. [1] With even these simple approximations it can be shown that there are tradeoffs between yield and selectivity, and that he preferred reactor design for a given system of reactions depends on both the specific reaction kinetics and the scale of operation.
A classic example of such an analysis is the Van de Vusse reaction system. [2] While insightful, idealized reactor models such as the CSTR and PFR cannot always be applied to real reactors, which can contain dead zones and recirculating regions, among other mixing imperfections, that affect the residence time of fluid elements. In these cases, numerical simulation of flow in the reactor is useful to improve understand the actual mixing pattern in the reactor and optimize reactor performance. COMSOL Multiphysics® simulation software enables the simulation of both flow and kinetics to investigate these nonlinear effects.
Additional complications arise when scaling reactors from lab to production volumes because mixing characteristics change during reactor scale-up. This means that large scale reactors may produce different product compositions than their lab scale counterparts. Understanding these differences is critical to designing large scale reactors. Here, we use COMSOL Multiphysics® to study the changes in mixing properties observed in reactor scale-up. Specifically, we focus on the laminar-turbulent flow transition and show how the associated change in mixing properties affects reaction yield and selectivity in the classis Van de Vusse system, and discuss the implications of the results on reactor design.
References
- Fogler, H. Scott. Essentials of Chemical Reaction Engineering. Pearson Education, 2010.
- Van de Vusse, J. G. "Plug-flow type reactor versus tank reactor." Chemical Engineering Science 19.12 (1964): 994-996.
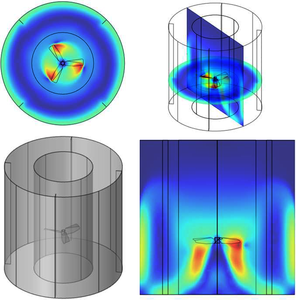
Download
- fiore_chem2_presentation.pdf - 0.71MB