Numerical Analysis of Bubble Powered Micropump
Development of micro-pumps will allow the minimization of many mechanical, bio-engineered and electrical systems, for example: controlled drug delivery systems or liquid cooled microprocessors. The development of such system is facing two major challenges: the design of actuation mechanism and the flow direction control.
Many design concepts and prototype micro-pumps have been demonstrated over the past decade, such as: mechanical displacement, bubble, electro-hydrodynamic, and electro-capillary. For the flow direction control there is a use of micro valves or valve-less micro-pump by means of nozzle-diffuser design. In order to design high performances systems a modeling study must be done.
In the present work a numerical model was developed to simulate the operation of a micro-pump driven by bubble formation and growth. Each sub-model was separately evaluated with literature results: nozzle-diffuser steady state flow characteristic, 3D nozzle-diffuser displacement driven pump, spherical homogeneous bubble growth and finally bubble driven micro- pump.
The bubble pump actuation can be divided into stages: first the liquid is heated until critical saturation conditions for bubble formation are achieved. Following, the bubble grows and pushes the liquid from the pumping chamber toward the nozzle-diffuser system. After the heating stops the bubble collapse and new liquid enters the pumping chamber.
The model solves the time dependent conservation equation for viscid fluid: mass, momentum and convection heat transfer. The Level-Set method is being used, to represent the gas-liquid interface. The analysis is made by using finite element software COMSOL Multiphysics®, the model code was written and activated using MATLAB® .
The equations for homogeneous bubble growth model were modified in order to describe correctly the connection between heat and mass flows on bubble interface. The model was compared with analytical results and showed good correlation.
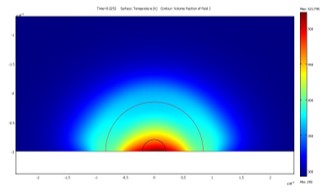