Thermal and Flow Simulation of a High Temperature Printed Circuit Heat Exchanger
Printed circuit heat exchanger (PCHE) is a key component in many energy and power systems, such as concentrated solar power plant, nuclear power plant, aircraft, etc. In this paper, the thermal and fluid performance of a lab-scale PCHE is analyzed using COMSOL Multiphysics® simulation software. The PCHE is made of a robust dense ZrC/W-based composite. The hot stream fluid is molten salt and the cold stream fluid is supercritical CO2 (sCO2). The system pressures on hot and code sides are 0.1 MPa and 20 MPa respectively. The inlet temperature is 720°C for molten salt and 500 °C for sCO2. The lab-scale PCHE contains five plates for molten salt flow and five plates for sCO2 flow. The plate dimension is 150 mm x 90 mm x 3 mm. The channel diameter for both molten salt and sCO2 channels is 2.5 mm. Unlike most of existing PCHE studies which only simulate one channel and apply periodic boundary conditions, the whole PCHE geometry is simulated in the current work. This can produce more accurate results about the PCHE performance by avoiding oversimplifying the geometry and making too many assumptions. The 3D drawing is made in SOLIDWORKS®
, and then synchronized into COMSOL Multiphysics® using the LiveLink™ for SOLIDWORKS®. For flow simulation, the Laminar Flow interface is used for molten salt flow and Turbulent Flow interface is used for sCO2 flow. The Heat Transfer interface is used for both solid and fluid domains. Two Nonisothermal Flow multiphysics interfaces are used to couple Laminar Flow with Heat Transfer, and Turbulent Flow with Heat Transfer interface, respectively. Meshing is very challenging for the whole heat exchanger simulation because the overall scale is two orders of magnitude larger than the smallest scale. Automatic meshing turns out to be not a good option for this complicated simulation domain. A user-controlled mesh is generated which is fine enough to capture the change of physics and course enough to keep the computational cost affordable. The velocity, pressure, and temperature field in the PCHE was solved from the simulation. The pressure drop, heat transfer coefficient, and thermal efficiency was obtained. The flow field in the header region is also helpful in providing insights to optimize the header geometry to better distribute the flow form header to channels.
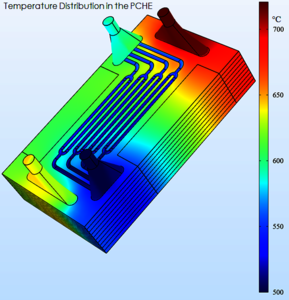
Download
- zhu_cfdfsi_presentation.pdf - 7.41MB