COMSOL Now Blog Posts
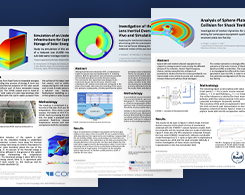
Best Papers and Posters from the COMSOL Conference 2023 Munich
Electrochemical deposition, energy geostructures, and laser welding are just a few of the topics featured in the top papers and posters from the COMSOL Conference 2023 Munich.
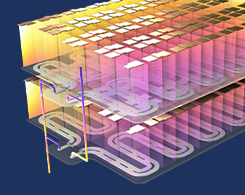
Multiphysics Modeling and Standalone Simulation Apps Drive Innovation
See why your organization should consider making the latest version of COMSOL Multiphysics® part of your R&D workflow.
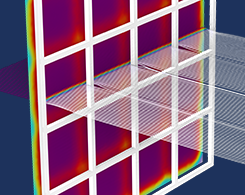
Version 6.1 Is Here: What’s New in the Latest Release of COMSOL®?
COMSOL Multiphysics® version 6.1 introduces new functionality for detached eddy simulation, satellite thermal analyses, robust mechanical contact modeling, and more.
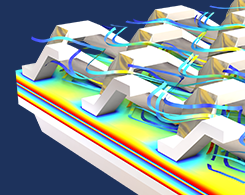
Now Available: COMSOL Multiphysics® Version 6.0
COMSOL Multiphysics® version 6.0 introduces the Model Manager, the Uncertainty Quantification Module, and many significant updates throughout the product suite.
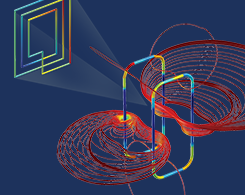
The Growing Use of Simulation in the Biomedical Industry
From implants and stents to MRI and spinal cord stimulation, numerical modeling is paramount to biomedical device development. Learn more and hear from key players in this industry.

2020 Isaac Newton Medal and Prize Awarded to Nader Engheta
Get an overview of the Isaac Newton Medal and Prize — and the optical physicist who won this year.

Keynote Video: Rapid Prototyping for Sonar Systems
Engineers at Northrop Grumman follow a 4-part rapid prototyping design phase: Design, manufacturing a prototype, testing and design verification, and manufacturing of the final design.
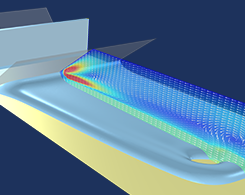
COMSOL Multiphysics® Version 5.6 Is Now Available
COMSOL Multiphysics® 5.6 brings faster solvers, enhanced graphics, and 4 new products: the Fuel Cell & Electrolyzer, Polymer Flow, and Liquid & Gas Properties modules and LiveLink™ for Simulink®.