Fermentation in Beer Brewing
Application ID: 27281
An important step in brewing beer is the fermentation process. Here, alcohol is formed together with various flavor substances from sugars in the presence of yeast. The initial sugar content, temperature, and yeast type dictate how the fermentation proceeds.
In this example, the fermentation process is efficiently modeled using the Reaction Engineering interface, assuming that the reaction rate is neither mass- nor heat-transfer limited; that is, the system is perfectly mixed. The example reproduces results in Gee and Ramirez[1], and in Ramirez and Maciejowski[2].
References:
D.A. Gee and W.F. Ramirez, “A Flavour Model for Beer Fermentation,” J. Inst. Brew., vol. 100, pp. 321–329, 1994.
W.F. Ramirez and J. Maciejowski, “Optimal Beer Fermentation,” J. Inst. Brew., vol. 113 (3), pp. 325–333, 2007.
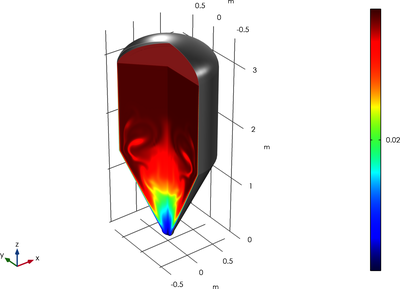
This model example illustrates applications of this type that would nominally be built using the following products:
however, additional products may be required to completely define and model it. Furthermore, this example may also be defined and modeled using components from the following product combinations:
The combination of COMSOL® products required to model your application depends on several factors and may include boundary conditions, material properties, physics interfaces, and part libraries. Particular functionality may be common to several products. To determine the right combination of products for your modeling needs, review the Specification Chart and make use of a free evaluation license. The COMSOL Sales and Support teams are available for answering any questions you may have regarding this.