3D Modeling and Analysis of a Mock-up Ironless Stator Design for Electrical Machines
With the evolving trend of electrification in transportation, electric machines with higher power density and higher efficiency are demanded which results in the thermal limit of the stator winding becoming more of a key constraint. The achievable current density in stator windings is limited by ohmic and eddy current losses in the conductor. Excessive conductor heating not only limits allowed current density, but also strains the electrical insulation needed in coils and adversely affects the reliability and meantime-between-failure. In fact, insulation breakdown of stator windings constitutes the major failure mode of electrical machines. Since the electrical resistance of copper increases rather rapidly with temperature, effective cooling is mandatory to enable high power density and high reliability. For this study, a dual rotor motor is considered allowing for the implementation of a ironless stator winding with direct cooling. Direct contact between the coolant and the conductor leads to unprecedented cooling efficiency and current density and enables significant overload capacity of the stator windings, facilitating, for example, the hovering phase in eVTOL aircraft applications. For many applications this should also eliminate the need for redundant phase windings thereby further increasing possible power density of the machine. A COMSOL® model was developed to simulate a mock-up stator design (1 pole and 1 phase) to find the peak/max temperature of the stator after reaching steady state and compute the pressure loss across the stator. The model uses the Computational Fluid Dynamics (CFD) and Heat Transfer Modules and the k-e formulation was used for solving the turbulent flow model. As part of the modelling a parametric analysis was performed to study the effects of the peak/max temperature of the stator for different mass flow rates of the coolant and current densities. Air is used as the coolant and PEEK and Alumina are used as stator support material. A litz wire with a filling factor of 0.7 is used as the conductor and helps in minimizing the eddy currents in the stator. COMSOL Multiphysics® was used in this study because of its ability to perform multiphysics simulations, handle highly non-linear problems and its parametric analysis capabilities. The simulation results will be compared to measurements performed on a sub-scale mock-up stator winding.
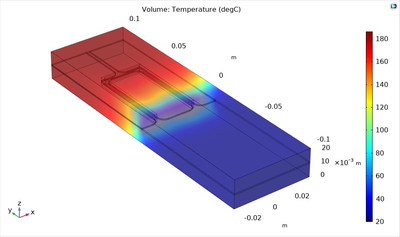
Download
- COMSOL Poster-TA-PJM.pdf - 0.39MB
- COMSOL Paper -TA-PJM.pdf - 0.79MB