Actuation Force Study of Next Generation Micro Shutter Array for More Reliable Actuation
Micro shutter array (MSA) is a programmable optical spatial filtering device fabricated by micro electro-mechanical system (MEMS) technology. It was originally developed for James Webb Space Telescope (JWST) to enable multi-object spectroscopy and operated by a moving magnet. Next Generation Micro Shutter Array (NGMSA) is an effort to improve JWST MSA by eliminating macroscopic moving actuation magnet and using electrostatic force to achieve more simple and reliable instrument that can support NASA’s multiple future missions.
NGMSA is a 2-dimensional array of unit shutter with size of 100 x 200 µm. A unit shutter is consist of silicon frame, shutter blade and torsion bar. Both shutter blade and torsion bar are made of silicon nitride/aluminum bi-layer. Each shutter blade is suspended to the frame by a pair of symmetric and collinear elastic torsion bar which twists as shutter blade actuates. Actuation of shutter blade is defined by electrostatic force applied on shutter blade and torsion bar’s restoration force.
We have been fabricating NGMSA with design inherited from JWST, however the legacy design is not friendly for electrostatic actuation because applied force direction on the moving shutter blade is different. We use COMSOL Multiphysics® simulation software (the AC/DC Module’s Electrostatics interface) to understand electrostatic force applied on an individual shutter within a range of motion and study new candidate designs. Also, structural mechanics module is used to study torsion bar’s restoration force.
Two different geometries are used for electrostatic model and solid mechanics model. In electrostatic model, half of a unit shutter with a symmetry plane and surrounding air geometry is used to calculate torque on shutter blade. Electric potentials are defined on blade and frame’s top surface (column electrode), back wall and frame’s bottom surface (row electrode) and the other frame surface (frame electrode). Domains adjacent to blade are defined for symmetric mapped mash for accurate electrostatic force calculation. Infinite element domains are introduced to mimic infinite air surrounding the shutter geometry. The shutter blade and surrounding domain’s angle is set as a parameter and parametric sweep function is used to calculate torque in entire motion range.
In solid mechanics model for torsion bar, a simple bar geometry that represent half torsion bar is used. One end of the bar is fixed and the opposite end is set for roller boundary condition to ensure that length of the bar does not change. Parallel and opposite directional boundary forces are applied on roller side of the bar to apply torsional force. The force is parameterized and applied with incremental increase by each step.
Result from two models shows that electrostatic torque with current design is difficult to reach high enough to overcome torsion bar’s mechanical restoration force near 20 degree position. Main problem is proximity between frame and moving end of shutter blade, which is only 2 µm. New candidate designs with shorter blade (wider gap) are studied using same electrostatic model. We figure out that shutter blade with 2-3 µm shorter blade can be actuated much easier compared to current design
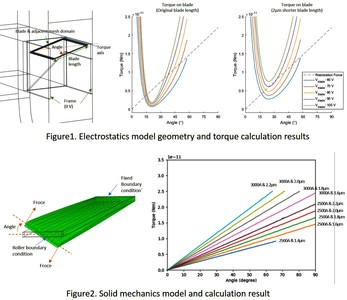
Download
- kim_poster.pdf - 1.32MB