An Innovative Solution for Water Bottling Using PET
Introduction: We study an innovative technology for water bottling using PET, aimed at reducing the thickness of the plastic bottles. The goals are the reduction of the amount of plastic used for a single water bottle, the reduction of the packaging costs and more environmental sustainability. The required thickness of the bottle depends on its structural function: when carried, the bottles are piled one on top of the other and, consequently, they are subject to a mechanical loading. Our innovative solution is to introduce in the bottle a suitable amount of pressurized inert gas in the free space over the water. The pressure of this gas partially balances the external loads, and thereby the thickness of the bottle can be reduced. Here, we study the structural behavior of a particular thinner pressurized bottle, and then analyze the effectiveness and the criticality of this lay out. Use of COMSOL Multiphysics: Our problem is highly nonlinear: the pressure of the gas depends on the volume of the bottle and therefore on its deformation, but the deformed shape of the bottle depends itself on the pressure of the gas and on the external loads; moreover, the slenderness of the PET walls requires a nonlinear kinematic [1,2]; finally, we have two phases in mutual interaction. Using COMSOL Multiphysics, the solid phase is described by the Shell module considering geometric nonlinearity; the relationship between the pressure of the gas and its volume is described by a thermodynamic process [3]. An integral probe calculates the volume taken by the gas; this probe works on the volumetric deformed mesh that is updated by the Moving Mesh module. The geometry and the adopted mesh are shown in (Figure 1). Results: For evaluating the deformed volume of the pressurized bottle before applying the external loads, we first consider a constant pressure of the gas (20,000 Pa) in absence of external loads (Figure 2). Then, the nominal load (9,4 daN) is applied on the cap of the bottle while the pressure of the fluids is linked to the deformed volume (Figure 3). Two conditions are checked: 1) the stress in the PET must not exceed the yield limit, for avoiding residual deformation of the bottle; 2) the bottle under load must not reach conditions of structural instability, that implies its collapse. The effectiveness of the proposed solution is highlighted through the last analysis: if we set the gas at the atmospheric pressure, the bottle does not support the load and implodes, loosing its stability (Figure 4): without the pressure of fluids, more thickness is needed for carrying the nominal loads. Conclusion: Advanced multiphysics simulations may give great advantages in the analysis of complex problems like the one above sketched. The effectiveness of the model allows us to further improvements, based also on some tests on prototypes of the bottle, and on gradient-based optimizations aimed at finding the optimal shape of the bottle and, at the same time, the optimal value of the internal pressure of the gas.
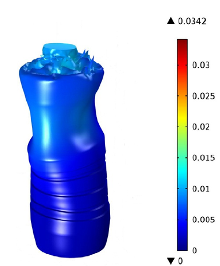
Download
- fraddosio2_presentation.pdf - 0.98MB
- fraddosio2_paper.pdf - 1.01MB
- fraddosio2_abstract.pdf - 0.22MB