Analysis of Powertrain Mounting System
Powertrain mounting systems are subjected to varying degrees of continuous dynamic loads resulting into unbalance of forces at their mount locations. These forces contribute significantly towards noise, vibration and harshness signatures in the vehicle cabin and has strong negative correlation to the vehicle occupant comfort. Hence it is critical to isolate the powertrain components from the vehicle body effectively to reduce transmission of force perturbations.
The traditional approach to perform the detailed analysis using dedicated MBD tools is often time consuming and limited to few iteration loops. It is observed that usually mount selection and its stiffness tuning, rather than its detailed design is actual problem faced by the powertrain integration engineers.
To address this issue, an application to predicts the basic performance parameters of powertrain mounts, the natural frequencies, relative displacements and angular rotations, was built using the COMSOL Multiphysics® tool. This app can simulate the performance of three-point and four-point mounting system. The app uses the Multibody Dynamics and Structural Mechanics module of COMSOL Multiphysics®.
For each mount, coordinates and stiffness data is given as input. If available, designer can input dynamic stiffnesses as a function of displacements. Powertrain data required for simulation includes its mass, six components of mass moment of inertia tensor and load vector.
The app is deployed on internal enterprise level calculation portal “MathApps” and can be run in a web browser remotely.
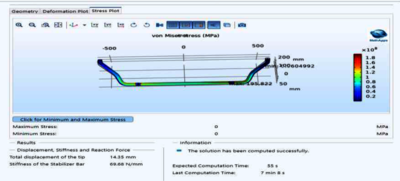
Download
- Fulkar.pdf - 0.5MB