Baffle Design: Tube-in-Shell Electrical Gas Heaters
It is frequently necessary to electrically heat gases; a convenient geometry is the familiar tube-in-shell heat exchanger, where the tube side is modified for electrical heater-rods, and the baffled shell side contains the flowing gas, as indicated in Fig. 1. However, this modification changes the essence of the thermal boundary conditions near the baffles from being temperature-limited to being flux-limited; special detailed considerations are then necessary to avoid burn-out.
In this work, two- and three-dimensional analyses are performed using a COMSOL Multiphysics® simulation. Heat transfer from the heater rods to the tubes is by radiation, and turbulent fluid flow is modeled for the shell-side gas using the k-epsilon turbulence theory. Special, thru-flow baffles are designed to limit local temperature hot-spots, and to maintain the tube spacing. Novel inlet conditions are designed and evaluated to accomplish beneficial flow development. The tie-rods that are always provided in shell and tube exchangers to position and support the baffles are further used to improve heat transfer by providing increased axial velocity.
The results show that the serpentine flow design of a typical shell and tube heat exchanger is inherently unsuitable for electrical heating, and can lead to burn-out issues; however, the COMSOL modeling shows that converting to well-distributed axial flows solves these issues. Also, establishment of the distributed axial flow down the exchanger is studied in detail; it is shown that proper inlet and outlet baffle designs can produce a “turning baffle” which converts the sideways inlet and outlet flows to smooth axial flow down the heat exchanger length.
The detailed radiation analysis showed that the tie-rods also provided an “extended area” surface which could provide further heat transfer. This extended area is unique in that the mechanism of heat supply to the extended area is via radiation rather than conduction as in a conventional fin.
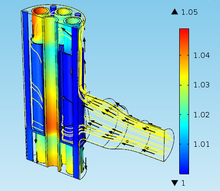
Download
- lund_presentation.pdf - 0.96MB
- lund_paper.pdf - 0.71MB
- lund_abstract.pdf - 0.12MB