Calculating the Dissipation in Fluid Dampers with Non-Newtonian Fluid Models
Introduction Present paper gives a comparison of the Upperconvected Maxwell (UCM) and the Oldroyd-B model for the calculation of dissipation in high shear-rate cases of viscodampers. When polymeric liquid is considered that part of energy that is irreversible can not be calculated in the typical way. For fluids where the separation into a solvent and a polymer part is not available the deformation gradient tensor must be separated into two parts.
Use of COMSOL Multiphysics®
To implement the UCM model into the FE model custom PDEs were used. In order not to rewrite the equation of fluid flow some parts have been eliminated and others have been added. The non-Newtonian material model is attached as a source term. Due to high shear rates heat generation plays an important role in the modeling process. This coupling is easily achieved using COMSOL Multiphysics® software. Both CFD and heat transfer are considered and PDEs are also used.
Results
For the calculations the original 3D device was simplified to an axial symmetric model. The inner channel containing the fluid was also simplified.
In Figure (1) the viscous dissipation can be seen. It shows that the energy increases towards the radius. In Figure (2) the dissipation can be seen as a function of time at the point marked a red plus sign. For the non-isothermal calculation the averaged value is used as an internal heat source as a function of radius.
In Figure (4) the simulation results are compared to the data from measurement. The measuring points of the damper are on the outer face of it. The results are correlated to the temperature values set by measurement, this is the reference temperature. One can see that both the UCM and Oldroyd-B models give very close results to the reference data. As expected the Maxwell model gives significantly higher values, because this is not suitable material model for computing the dissipation in damper fluids. For ease of use the UCM model is a good choice in sense of engineering calculations. Especially in the computation of heat transfer computations.
Conclusion
In this paper non-Newtonian material models were compared for the calculation of viscous dissipation. In COMSOL equation based modeling is available to use custom equations. After coefficient matching the non-linear material models can be easily implemented into the software. In the studied device more than one physics is needed to properly investigate the effects of different materials. Coupling these is just a few clicks and switching between the material models needs minimal effort.
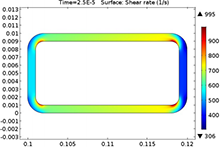
Download
- forberger_presentation.pdf - 1.25MB
- forberger_paper.pdf - 0.82MB
- forberger_abstract.pdf - 0.88MB