COMSOL Multiphysics® Model for Optimizing Regeneration of CFP Catalyst in Packed-Bed Reactors
The DOE BETO consortium "ChemCatBio" has developed a packed bed catalyst for use in a Catalytic Fast Pyrolysis (CFP) process for producing biofuels and chemicals from lignocellulosic biomass. Another BETO consortium known as "CCPC" (Consortium for Computational Physics and Chemistry) is supporting this objective using advanced, first-principle modeling spanning all scales: atomic, meso and process. In one element of the process scale program, COMSOL Multiphysics® simulation software is used to model regeneration (coke combustion) of the packed bed catalyst, using real 3D reactor geometries, catalyst properties, operating conditions and transient behaviors. Because of the exothermic nature of coke combustion, regeneration has been determined to be the most critical process step. Done poorly, regeneration can lead to variations in stresses in the particles, which can lead to particle degradation and reactor shutdown. Also, deactivation of dispersed catalyst phases via Ostwald ripening can occur to different degrees depending on local time-temperature environments. The objective for the COMSOL Multiphysics® model is to address both of these issues, and others.
The COMSOL Multiphysics® regeneration model makes use of the Reactive Pellet Bed feature, which adds an extra dimension to capture intraparticle transport mechanisms. This is augmented using the Chemical Reaction Engineering Module, as well as the appropriate fluid flow, heat transfer and dilute species transport interfaces, for modeling the combustion reactions of carbon and hydrogen in coke. In all cases, the approach is to describe real reactors and catalysts as accurately as possible under the project timeline.
To calibrate unknowns in the COMSOL Multiphysics® regeneration model, the first step was to build and tune accurate models of a small lab-scale CFP reactor system currently being operated at the National Renewable Energy Lab (NREL) in Golden, Co. This system, known as the "2FBR", contains approximately 100 grams of catalyst in the packed bed CFP reactor. In this system, regeneration occurs every 3-8 hours, and takes between 30 minutes and 2 hours. Successful validation of the 2FBR model, including kinetics and thermal effects, will be shared in the presentation.
The second step is to use the 2FBR learnings to build a model for a pilot-scale reactor at NREL known as the "TCPDU". The packed bed reactor in the TCPDU is slated to use 25 kg of catalyst: a scale up factor of 250. The presentation will share the current status of the COMSOL Multiphysics® model for accomplishing this scale up - specifically, with respect to optimizing the catalyst loading and regeneration procedures to minimize the aforemention mechanical stresses and nonuniform catalyst deactivation. Also, the model will be used to design the overall swing process, in which the regeneration step is integrated with the conversion step.
Finally, the presentation will close with a look forward to the next phase, where the model will be extended to include CFP performance, using experimentally-obtained reaction models and kinetic expressions. As part of this look-ahead, our vision for an integrated approach using the model in future ChemCatBio packed bed development work will be illustrated.
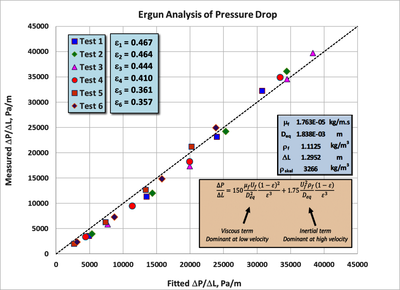
Download
- adkins_chem1_presentation.pdf - 2.94MB