External Corrosion Modeling for an Underground Natural Gas Pipeline Using COMSOL Multiphysics® Simulation Software
This paper studies external corrosion of an underground transmission pipeline carrying natural gas. Pitting corrosion and Stress Corrosion Cracking (SCC) are two most common external corrosion types for buried pipelines and they usually happen when the mitigation methods such as coating or impressed current cathodic protection (ICCP) fail or deteriorate. Pitting corrosion is a localized corrosion which occurs at sites with no coating or cathodic protection as a result of electrochemical reaction between the pipe material and a corrosive environment, while SCC is a joint action of a corrosive environment and tensile stress from the soil movement. A finite element model was developed in COMSOL Multiphysics® simulation software to study the relationship between corrosion potential, current density, and Von Mises stress along the corrosion defect as a result of near-neutral pH SCC using the Corrosion interfaces and Structural Mechanics Module. On the other hand, pitting corrosion is simulated by the Caleyo et al.’s model, which calculates pit growth rate based on several operating inputs. Multiple sensitivity analyses were performed to find the relationship between the defect depth, defect length, and the soil stress with respect to anodic current density, cathodic current density, and corrosion potential in order to obtain corrosion rate for SCC. In addition, another set of sensitivity analyses were performed to find the relationship between the soil resistivity, bicarbonate ions concentration ([HCO3-]), pH level of the soil, chloride ions concentration ([Cl-]), water content of the soil, sulphate ions concentration ([SO42-]), pipe/soil potential, bulk density of the soil, and redox potential with respect to corrosion rate for pitting corrosion. The SCC results show that the maximum corrosion potential decreases with the increasing defect depth, but increases with increasing defect length, and that the maximum von Mises stress increases with increasing defect depth but decreases with increasing defect length, which indicates that the corrosion is most severe at the center of the defect.The results of this paper will be the input to a Bayesian Network model which calculates the probability of pipeline failure in terms of external corrosion. This model is composed of three layers, namely corrosion, mechanical, and reliability models. The corrosion models include pitting corrosion and stress corrosion cracking. The output of this model will be the corrosion depth based on the corrosion rate results of this paper. The mechanical model calculates the remaining strength of the pipe given the dimension of the defects and will be used in the reliability model for probability of the pipeline failure calculation.
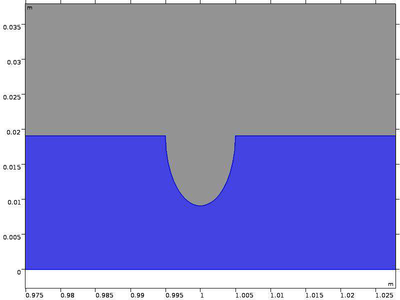
Download
- chalgham_paper.pdf - 1.81MB
- chalgham_chem2_presentation.pdf - 1.32MB