Modeling the Hyperloop with COMSOL®: on the Mechanical Design of the EPFLoop Capsule
The Hyperloop is a concept system targeting passenger transportation aiming to carry people in a pod running in a high vacuum tube at 1200 km/h. In 2015, SpaceX announced that they would sponsor a Hyperloop pod design competition, because of their interest in helping to accelerate the development of a functional Hyperloop prototype. The EPFLoop team (http://hyperloop.epfl.ch/) has been formed on September 2017 at EPFL with the intention of participating in third edition of this competition that took place in July, 2018. It groups PhD, master and bachelor students in a highly innovative environment that tackles the future of transportation. This year, over 5000 teams applied in October to participate in the competition and only 20 teams passed the final selection. The EPFLoop team is proud to be one of the teams in the final round.
The design of the mechanical subsystems, such as the chassis, the stability system and the braking system was one of the many technical challenges of the project. Indeed, these components are fundamental to ensure the high performance and the safety of the pod. The aluminium chassis is the main structural skeleton, providing the connection among the various parts of the pod. In particular, it has to withstand the loads that are given by the subsystems (pressure vessels, aeroshell, motor, etc) due to the initial acceleration and final deceleration. Since the acceleration and deceleration values are almost constant, the chassis nominal load has been studied using stationary simulations in the Solid mechanics module. To avoid instability phenomena, a linear buckling failure has been devised as well. The results show a maximum stress state for the loaded chassis which is less than the material’s strength and a safety factor greater than 2 everywhere, as required by the competition rules. The pod runs on a 1.2 km rail, composed by numerous short sections. Passing from a rail section to the next, the pod could experience a sudden deviation, both in the vertical and horizontal direction, due to possible misalignments. Therefore, a stability system has to be devised and tuned to avoid any possible resonance. For this study, the Multibody Dynamics Module has been used. Firstly, the chassis structure has been considered as rigid, with the masses of the subcomponents concentrated at their attachment points. Then, the wheel and suspension components were modelled as lumped mechanical systems. The results provided clear indications on the principal modes of vibration and on the required tuning of the stability system.
Finally, the braking system has been studied. To ensure that the temperature profile during the deceleration phase does not exceed a threshold above which the material would degrade its properties, a time-dependent Heat Transfer in Solid simulation has been carried out, coupled with a material sweep. The result showed a temperature increase of 400 °C and allowed the team to choose the proper material for the braking pad. The chassis and other subsystems of the EPFLoop pod will be exhibited at the COMSOL Conference Lausanne 2018.
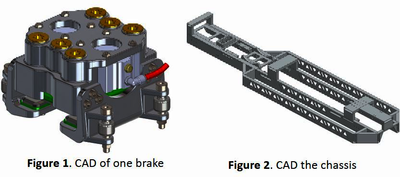
Download
- riva_presentation.pdf - 8.94MB
- riva_poster.pdf - 1.47MB
- riva_abstract.pdf - 0.15MB