Modelling of Pressure Profiles in a High Pressure Chamber using COMSOL Multiphysics
High Pressure Processing (HPP) is a leading non-thermal food processing technology that is often cited as a major technological innovation in food preservation. Although it is very early to place this emerging technology among the list of breakthroughs in food processing, HPP has started to become a viable commercial alternative for pasteurisation of value added fruits, vegetables, meat, and seafood products to be safely enjoyed by the consumer. In a High Pressure process, the food product to be treated is placed in a pressure vessel capable of sustaining the required pressure; the product is submerged in a liquid which acts as the pressure-transmitting medium. The working pressure for any HP process is a very important parameter, not only because the capital investment of such an equipment increases steeply with increases in working pressures, but also because a decrease in working pressure can reduce significantly the number of failures, increasing the work life of the equipment (Otero et al., 2000). The objectives of this study were to model the stress profiles in a High Pressure chamber, modelling of Temperature – time plots in a High Pressure chamber using COMSOL 4.2a and understand the yield criteria for the vessel and the temperature gradient in the vessel with time in the presence of a constant heat source. In the current research, a pressure of 200 MPa was applied internally to an empty pressure vessel initially. Subsequent to that, a polyethylene core was introduced into the vessel’s core and the same internal pressure of 200 MPa was applied. The Von Mises stress produced in both the cases was different owing to the introduction of the polyethylene core. A plot showcasing the change in the Von Mises stress with changes in operating pressure was plotted later on. Studies of the changes in the temperature of the vessel with changes in operating pressure were also made and have been depicted pictorially. The changes in the temperature of the vessel were of the order of 10K at an operating pressure of 300 MPa in a time span of about 120s. The results obtained as part of this study were primarily profiles that are time independent as well as dependent as the case maybe. The stress profiles were obtained with increase in working pressure in the vessel. The Temperature–Time plots were for a fixed working pressure applied for a time duration of 120s. The increase in the Von Mises stress in the case of an empty pressure vessel and upon the introduction of a polyethylene core was in accordance with the theoretical background of HP processing. Depending on the material used in the manufacture of the vessel, the yield point of the vessel varies. The Von Mises stress is an important parameter that is used to find the operating pressure that a certain vessel can withstand without fatigue or failure. This study emphasises the importance of such an analysis and the use of COMSOL Multiphysics for the same.
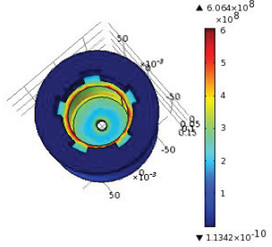
Download
- rao_presentation.pdf - 1.11MB
- rao_paper.pdf - 0.43MB
- rao_abstract.pdf - 0.14MB