Multiphysics Simulation for Different Topology of Heat Sink Design
In recent times, the major concern in the area of microelectronics is efficient heat transfer which will improve the operating characteristics of the device as well as minimize its failure rate due to induced overheating. The removal of excess heat from the system can be done by conventional heat sinks. Thus, heat sinks can be effectively used to increase the less efficient Thermoelectric coolers so that their overall Coefficient of Performance (COP) can be improved. The typical thermoelectric coolers have low COP of 0.3-0.5 at an operating temperature of 5 °C at an ambient temperature of 25 °C. As found in the review literature of thermoelectric cooling [1], a good thermoelectric material needs to be chosen in such a way that the temperature difference between hot side and cold side of the Peltier module needs to be minimized for a significant COP. The objective of this paper is to analyze the effect of various fin configuration design of the heat sink model on cooling performances. In this study, the multi-physics software COMSOL® has been chosen for computational fluid dynamics (CFD) analysis. This software can be used proficiently to investigate the heat transfer and fluid flow characteristics for various designs of the heat sink. The fluid flow and heat transfer characteristics of a 3-D heat sink are obtained numerically by solving the appropriate governing equations using the COMSOL® software. The numerically predicted results obtained through this can be validated later with the experiments using the dependent variables used in simulation as it is. Hence using COMSOL® software, we have simulated results using different types of materials for a heat sink with different physical arrangements viz. multiple perforations or creating rough surfaces so as to increase surface area to facilitate the heat dissipation promising an increased COP. The assumptions made to simplify the simulation process can be listed below: 1. Steady state heat transfer 2. Incompressible fluid (air) 3. Laminar flow 4. Uniform wall of heat flux 5. Constant solid and fluid properties 6. Negligible radiation of heat transfer For CFD analysis, the heat flux applied for different models ranging from 10W/cm2 to 20 W/cm2 and inlet velocity varied from 0, 1 and 2 m/s. The defined material property for the heat sink is this study is aluminium and copper with and without perforations. The simulation result shows the inverse relationship between temperature on the heat sink and inlet velocity. The result shows that by increasing the total surface area, heat transfer increases. Thus, considering a rough surface for the heat sink, better heat transfer rate can be expected.
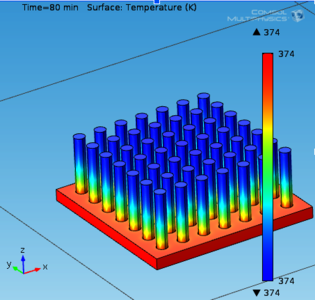
Download
- kumar_poster.pdf - 1.21MB
- kumar_paper.pdf - 0.73MB
- kumar_abstract.pdf - 0.08MB