Multiphysics Simulation of 2nd Generation 238Pu Production Designs Using the COMSOL Multiphysics® software
In order to qualify experiments for in-vessel irradiation at the High Flux Isotope Reactor (HFIR) at Oak Ridge National Laboratory, safety assessments need to be completed and documented to ensure adequate target cooling and structural integrity. Previously, finite element analysis tools have been used to simulate the appropriate phenomena for targets containing neptunium dioxide in aluminum pellets (NpO2/Al) and their irradiation over three HFIR operating cycles to produce 238Pu. 238Pu is used as the principal radioisotope used power source for NASA deep space mission and space exploration vehicles and target fabrication, irradiation, and chemical processing at ORNL are serving a critical function in re-establishing the domestic supply of 238Pu. The production designs assessed previously have been updated, including both the target pin and the target holder, which holds seven target pins, to a “2nd Generation” design. The unique design of the new target holder requires new methodologies and tools to both act as a design-aid tool and to re-assess individual target pin safety margin with regard to target cooling.
The COMSOL Multiphysics® software has been the principal analysis tool used to assess steady-state heat transfer and thermal stresses in targets for all experiment phases of 238Pu production. Its use in previous applications, and continued use in this case, has included the Heat Transfer and Structural Mechanics Modules by way of the coupled physics interfaces heat transfer in solids and solid mechanics, with contact pairs and thin layers used to model the non-linear effects of contact and gap conductance equations, in a 2-D R-Z geometry. The CAD Import and Design Module features are used to import new designs and modify for simulation using CAD repair features. The CFD Module is used to assess the 3-D target holder and pins in order to assess flow performance of differing designs both as a design-aid and for experiment comparison, and to assess the 3-D target cooling at the target pin clad, coupled with the heat transfer in fluids interface. The Pipe Flow Module was used to assess transient target cooling along with a 3-D representation of the target clad in the heat transfer in solids interface and couplings using general extrusion operators.
The CFD Module was used to successfully model flow performance for the differing flow paths in the 2nd generation target holder (see the inlet pressure drop and flow paths in the included figure) with successful validation against experimental results. The coupled 3-D convective cooling analysis of individual targets was then used to assess target surface cooling for differing flow positions and supply worst-case heat transfer coefficients into the 2-D R-Z thermo-mechanical model of a target pin, which further assessed cooling and structural integrity. The pipe flow module used the same inputs to assess bounding transient conditions of a target pin. The final assessments of safety parameters including target surface temperature, maximum pellet temperature, and cladding strains were compared against the defined safety limits with sufficient safety margin under all worst-case conditions.
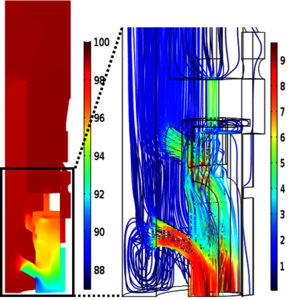
Download
- hurt_presentation.pdf - 1.62MB
- hurt_paper.pdf - 0.75MB
- hurt_abstract.pdf - 0.02MB