Multiscale Model of the PECM with Oscillating Cathode for External Geometries Using a Virtual Switch
The machining of hardened steel or powder metallurgical steel, for example to manufacture impact extrusion punches, is a big challenge for conventional machining technology as milling or turning. A non-conventional machining technology is Electrochemical Machining (ECM), which allows surface structuring and shaping of metallic workpieces with high accuracy and surface quality without wear of the tool electrode and independent of the mechanical properties of the workpiece. The machining principle of ECM is electrolysis. One variety of the ECM is the pulsed electrochemical machining (PECM) with oscillating cathode, which allows higher accuracy and better surface quality then the conventional ECM. The major challenge in applying PECM with oscillating cathode is the process design. In today’s practice, this is a time-consuming and cost-intensive iterative procedure. However, the efficiency of process design can be enhanced by applying computer simulations to calculate the workpiece shape or determine the process parameters. In the current state of research the PECM simulation models are performed with simplified assumptions to consider the pulsed direct current. This is a time efficient method, but it is not possible to analyze the physis phenomena like heat generation and hydrogen production during one oscillation period in a detailed approach. Furthermore, the PECM with oscillating cathode is a process which includes a considerable number of different physics phenomena with highly different time scales. Summarizing, PECM with oscillating cathode is a multiscale and multiphysics problem. In the present study, a multiphysics and multiscale model of the pulsed electrochemical machining with oscillating cathode of external geometries (Figure 1) is shown. This model combines two simulation steps in one comprehensive simulation, including short and long time scale phenomena. To perform this simulation a virtual switch, based on the PECM process parameter, is developed and implemented in COMSOL Multiphysics® using the Events interface and the PDE Interfaces. This virtual switch allows switching between the short and the long time scale phenomena without stopping the simulation and allows the correlation of the single physics phenomena and boundary condition to the respective time scale. The physics phenomena of short time scales are the electrodynamics, fluid dynamics, thermodynamics, the formation and transport of hydrogen and the oscillating motion of the cathode. The physics phenomena of long time scales are the material dissolution and constant feed rate of the cathode. This model helps to analyze the forming of the work piece and supports the process design for the pulsed electrochemical machining.
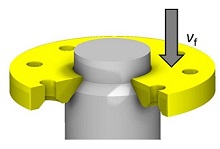
Download
- schaarschmidt_poster.pdf - 1.03MB
- schaarschmidt_paper.pdf - 1.67MB
- schaarschmidt_abstract.pdf - 0.03MB