Numerical Modeling of Airflow in Tissue Engineered Trachea
Life saving organ trachea has been tissue engineered in bioreactors. A dynamic bioreactor is a more suitable bioreactor for effective sustainability of a tissue engineered trachea. In this study, numerical modeling is performed for evaluating shear stress developed due to flow of various kind of air (including pollution free air, pollution rich air, aerosol, and smoke). Regions like active shear stress, moderate shear stress, and blind stress zones were identified from the numerical solutions of primary design of bioreactor-integrated scaffold. COMSOL Multiphysics® module like CFD, Microfluidics, Structural, Pipe flow modules were used to build the multi physics problem.
It was observed that differential stress regions lead to formation of lubricating layer of fluid of different thickness on the inner-wall of the synthetic trachea. It leads to difference in terminal mass of the implant, which converted to implant failure.
Thus, a new model of integrated bioreactor-tracheal segment design is proposed, and fluid flow parameters were evaluated in order to ensure improvement in shear force distribution throughout the surface of the scaffold. Intension of the design includes homogeneous distribution of shear forces. It had been observed that the new model developed enhanced stability of the implant when it comes fixation of the implant to parent organ site. Cyclic stress were also evaluated to measure the sustainability of the implant. Instead of a simplified model of tracheal segment, custom-made tracheal segment was used in the study, obtained from computerized scan data of diseased subject. The flexibility of importing irregular mesh geometry in COMSOL Multiphysics®
enhances the ease of the problem.
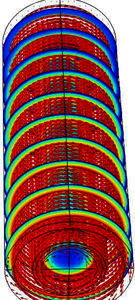