Optimum Design for Magneto-Rheological Brake Using COMSOL Multiphysics® Software
The Automotive industry has now become a technology of “Drive by Wire”. This technology is used to replace the conventional mechanical system by electromechanical system which is able to perform the same tasks faster, more reliably and accurately. The problems with the traditional braking systems are unreliable at high speeds, long respond time, more brake pad wear, high temperature operating conditions, pressure build up in the hydraulic lines, noise and bulky size. The proposed Magneto Rheological Brake (MRB) is an electronically controlled braking system. This allows easy implementation of software control systems, less number of components, simplified wiring, improved braking response time and generally optimized layout.
The MRB consists of rotating discs, which are enclosed by a static casing. The MR fluid is filled in the gap between the discs and casing. A magnetic coil is wound around the surface of the casing. When a low voltage current is applied on the magnetic circuit, the magnetic fields are generated and there is phase change in MR fluids that provides the required braking torque.
An MRB analytical model will be designed by considering the magnetic circuit, materials, sealing, working surface area, viscous torque generation, applied current density, MR fluid Selection.
The final design of the MR brake will result from an optimization procedure that uses the FEA models to study the performance and feasibility (temperature, power, size, weight and cost constraints) of the possible configurations. A suitable optimization technique will be selected for this purpose. The Optimum design is done through the Optimization Module COMSOL Multiphysics®. According to the optimum design the prototype model of Magneto-rheological brake was fabricated.
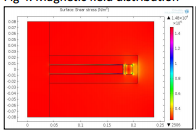
Download
- thanikachalam_poster.pdf - 0.46MB
- thanikachalam_abstract.pdf - 0.02MB