Parametric Analysis and Optimization of an Elastocaloric Heating and Cooling Cycle
Elastocaloric heating/cooling takes advantage of the structural changes in shape memory alloys (SMAs) that release and absorb heat when a strain is applied over a transition temperature. Heating/cooling cycles that use SMAs offer a potential solution to issues associated with the use of ozone-depleting refrigerants found in common heat pump/refrigeration cycles. Several recent works have found that the Coefficient of Performance (COP) for elastocaloric cycles is comparable to those achieved with standard HVAC systems of the same scale, which exhibit COPs of 3 on average. Conversely, SMA wires in lab settings have shown to achieve COPs as high as 3.5, and with sufficient optimization are expected to achieve COPs > 10 [1,2].
In this work, we explore the parametric space for optimization using COMSOL Multiphysics® to model the behavior of NiTi (an SMA) as strain is applied and released around a bend, where heat absorption and release occurs. We perform a parametric study that varies the wire radius, disk radius, its rotational speed, and its contact area with the primary heat sink. In order to simulate the continuous flowing of the wire over the disk, and appropriately capture the loss of heat to its surroundings, the wire and disk are modeled as fluids rather than solids. We use the Creeping Flow and Heat Transfer in Solids and Fluids interfaces to maintain a uniform flow, and adjust the thermal contact resistance between the disk and wire to reflect the temperatures measured by experiment across a range of parameters.
The Creeping Flow interface was used to simulate the movement of the wire as a rigid body solid rotating around the disk, while also providing flexibility to map specific thermal and mechanical behaviors of NiTi over the wire. Changes made to mimic this motion include applying a slip condition at the walls, driving the dynamic viscosity of the material close to zero, and applying linear and circular motion velocity fields on the straight and curved sections of the wire.
The Heat Transfer in Solids and Fluids interface was used to apply a volumetric heat sink and source at the bend of the wire. Two assumptions were made to model how heat enters the system: 1) Transformation in the NiTi takes place instantaneously, thus the sink and source are localized to only the regions entering and exiting the bend. After which, heat conducts through the wire and into the disk. 2) Though the latent heating would only occur within regions of the wire that are critically strained (at to 2%), the heat transfer is modeled uniform throughout the selected volume [1]. Sensible and latent heating characteristics of the strained region were used to model the equivalent volumetric heat release.
We expect these results to reveal the physical mechanisms that govern the performance of elastocaloric cooling cycles, including the parameters listed above. Such insight is critical to improving the performance of these systems in order to reach the theoretical maximum COP in small-to-medium sized heating and cooling systems.
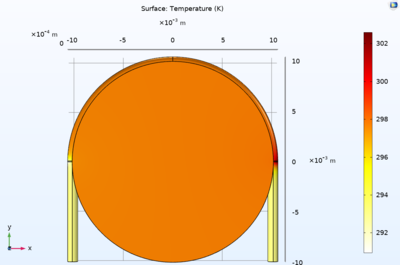