Simulation of Moisture Ingression in Microelectronics Packages to Correlate Test and Field Conditions
Plastic packages, coated with Epoxy Molding Compound (EMC) can provide an economic and versatile protection to the integrated circuits (IC) from mechanical damage. A major drawback of molded packages is that they are not hermetic and are prone to absorb moisture from external environment. Moisture is one of the principal causes of several package failure mechanisms: degradation of adhesion strength, popcorn effect during soldering and electrochemical corrosion are well-known examples. Moisture migrates through molding from external environment to silicon die, where it leads to corrosive reactions on metal layers of interconnections levels.
Many works use a physical model based on the phenomenon of diffusion of moisture in solid materials, which depends on the environmental conditions as well as on some material properties. Relevant diffusion properties are diffusivity and moisture saturation concentration, and they can be determined performing dedicated experiments on test samples under reference environmental conditions.
Purpose of this paper is to describe a series of simulations of moisture absorption in EMC under different test and field conditions, in particular THB (Temperature Humidity Bias) test, temperature 85 °C and relative humidity (RH) 85%, according to standard JEDEC JESD22-A101. The Application Library example “MEMS Pressure Sensor Drift Due to Hygroscopic Swelling” has been used as a reference to develop the model. As described in many works, moisture moving inside package can be approximated using Fick’s laws of diffusion, therefore using Transport of Diluted Species interface.
Starting from actual material absorption curves data provided by an EMC supplier, diffusivity and moisture saturation concentration are interpolated for a relevant range of temperature and RH conditions, and used as parameters for the simulations. The Heat Transfer in Solids interface is used to simulate different environmental conditions using in particular ASHRAE database for real world data. Results, in terms of moisture absorption as a function of time and in-package penetration depth are shown with focus on concentration at molding-die interface.
The model is then developed into multi-material simulations, adding an air gap between moisture and silicon die, to reproduce the effect of a delamination of the EMC. Delamination at the EMC-Die interface is not allowed by quality criteria, but current detection techniques are not able to detect the smallest voids (few µm thick) and so it is important to understand the impact of this worst case boundary condition on the above-mentioned phenomena. The so-called “normalization approach” is used to manage the concentration discontinuity at the interface of the two materials. Results from these simulations are also reported as described before.
The presence of the air gap also allows to make local evaluations of RH inside the package and to estimate the possibility of dew formation over die surface, in particular under dynamic test conditions like Thermal-Humidity Cycling (THC) tests. An acceleration factor based on total moisture absorption is also proposed to correlate accelerated tests with field life conditions.
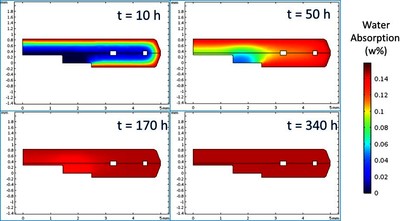