Simulation of Pilot Plant Fischer-Tropsch Reactor in Gas to Liquid Technology
Gas to liquid (GTL) technology can convert methane from the natural gas to liquid fuels and other valuable hydrocarbons which can then be quickly and efficiently transported. The catalytic Fischer-Tropsch (FT) synthesis is the most critical step of the GTL process, as it is in this step that high-value products are produced. The syngas (H2+CO) undergoes polymerization reaction in the presence of a catalyst (Fe/Co/Ru-based) to produce a wide range of products, like paraffins, olefins and oxygenates, often known as Syncrude. The reaction conditions play a crucial role in defining the product distribution. It is desirable to have heavier hydrocarbons (C5+) as a significant fraction, due to their commercial value, in the products. Low temperature (220-250 ℃), high pressure and low H2/CO ratio are the process conditions favorable to heavy hydrocarbon production. Design and operation of FT pilot-scale is presented in GTL plant. Developed kinetic model in two series of multi-tubular FT reactors over cobalt catalyst is considered and the commercial software package (COMSOL Multiphysics) is applied to simulate and predict the profiles of conversion and temperature in the reactor under a variety of conditions including different number of liquid hydrocarbons fraction, different inlet temperature, various coolant temperature, and non-uniform distribution of catalyst zone. To calculate the syngas consumption rate, proper developed kinetic model is used. Overall CO conversion of 50% and adequate temperature control applied in operating temperatures of 240 °C to 250 °C in the first step of multi tubular reactor. Moreover, the effect of coolant temperature and flow rate are evaluated to determine optimum operating conditions to achieve more conversion and higher heat flux to keep the FT tubes near to iso-thermal condition. COMSOL Multiphysics 5.3 was used for CFD modeling which has built-in mass, energy, and momentum modules in the simulation package. The primary aims of this study are 1) increasing efficiency of jet fuel and 2) definition of the proper kinetic model to predict the better behavior of FT reactor. The main challenge in designing FT reactor is choosing proper kinetic model with specific attention to the complexity of the reactions mechanism. Drastic increasing temperature through FT reactor took place at the entrance region of the reactors due to the high exothermic reactions. Isothermal and non-isothermal reactors are investigated in this study for different values of temperature in pilot plant dimension to get higher selectivity of jet fuel. Further simulation shows higher productivity and selectivity to control the FT packed bed rector near to isothermal conditions, appeared in the initial temperature of 249 °C.
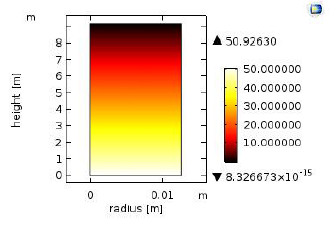
Download
- arabi_paper.pdf - 0.64MB
- arabi_abstract.pdf - 0.02MB