The Relevant Scale for Mechanical Modeling in Additive Manufacturing Technologies
Additive manufacturing technologies do not share the same rendering depending on the type of material discontinuities induced by material processing. This study aims at revealing the role of microstructural defects as driving factors for the mechanical performance of polymeric parts designed using fused deposition modelling. Structural mechanics module from Comsol software is used to predict the compression performance of 3D printed polymeric structures. Geometries of 3D prints are modelled using various forms of filament arrangements representing the effect of raster angle in fused deposition modelling 3D printing technology. 3D prints are considered as full dense materials or airy with amount and distribution of voids determined from topology optimisation module in Comsol software. The constitutive laws are implemented in a way to authorise the lack of adhesion between adjacent filaments and to induce damage depending on the load level. Simulation of severe compression levels is considered and the stress fields are analysed. Finite element results demonstrate the relevance of the filament scale as the geometric unit from which the model has to be built. The comparison between CAD-based and filament-based models clearly pinpoints the overestimation of performance from CAD-based models because of the underestimation of the process-induced porosity and the absence of inter-filament constitutive law. The fair agreement between the experimental results and predictions of filament-based computations promotes the use of structural heterogeneity as a genuine explanation for the unusual mechanical response of 3D printed structures. In addition, various deformation mechanisms put forward from the Comsol simulation are found to be supported by 3D imaging results based on X-ray micro-tomography. This study finally concludes that the regularity of porosity arrangement and its high connectivity are to be better controlled to improve the mechanical performance of additive manufacturing parts.
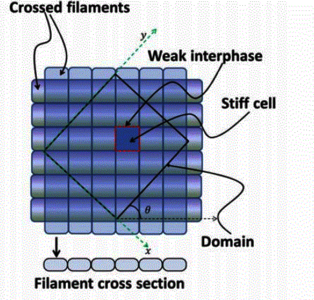
Download
- guessasma_presentation.pdf - 8.15MB
- guessasma_paper.pdf - 0.52MB
- guessasma_abstract.pdf - 0.4MB