Thermo-Mechanical Modeling of Laser Beam Welding of Molybdenum
Laser beam welding is a key technology in industrial manufacturing as it combines high flexibility and the potential for automation with excellent joint quality and minimal thermal influence of the workpiece. Whereas for materials like steel and aluminium laser beam welding is already widely applied in industrial fabrication routes, its application for the joining of high melting metals like molybdenum and tungsten is still in its initial stages. As refractory metals generally exhibit only limited weldability, in many high temperature applications, so far riveted joints are still widely applied. Apart from metallurgical issues that have to be solved for the fusion welding of refractory metals, the high melting temperatures and good thermal conductivities of these metals lead to high temperature gradients during the welding process, causing high residual stresses in the weld seam and consequently distortions of the workpiece. In this contribution a multi-physical thermo-mechanical modeling approach for laser beam welding of thin sheets in overlap configuration is presented. The multi-physical simulation model of the welding zone is shown in Figure 1 a. In the thermal model the energy input by the laser beam is modeled by a moving Gaussian heat source with exponential decay in the workpiece, approximating the absorption of the laser radiation in the vapour capillary. The heat transfer calculation takes into account latent heats of fusion and evaporation, respectively. The energy loss by evaporation is considered based on the Hertz-Knudsen formula. The thermal calculation controls the material and contact behaviour in the structure mechanical calculation. In the melt pool the material behaviour is approximated by a reduction of the elastoplastic material properties. The extend of the molten track, where material has molten and solidified, is tracked by a distributed ODE. Rigid contact between the joining partners in the molten track is modeled by a thin elastic layer. In the rest of the contact zone of the two sheets mechanical contact is defined. Clamping is modeled by spring foundations and boundary loads on the respective boundaries of the workpiece (see Figure 1 b). Based on the simulation model laser beam welding of molybdenum sheets in overlap configuration is analysed with respect to stress distribution and distortion of the workpiece. The results show how residual stresses in the molybdenum weld seam cause distortions of the workpiece after removal of the clamping (see Figure 1c). The presented simulation model can be applied in order to analyse the influence of different welding strategies on stress distribution and distortion in laser beam welding of thin molybdenum sheets.
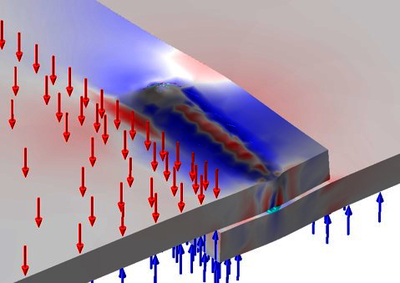
Download
- leitz_paper.pdf - 0.63MB
- leitz_abstract.pdf - 0.13MB