Thermomechanical Simulation of Equipment Subjected to an Oxygen Pressure and Heated Locally by the Ignition of Small Particles
In industrial oxygen systems at high temperature and high pressure, contamination by solid particles is one of the principal causes of ignition hazards.
Indeed, gas can sweep away particles, generated by corrosion inside the pipes or during maintenance operations (welding residues, careless disassembly, etc.) and produce accumulations at places where the gas velocity decrease.
Moreover, in such an environment rich in oxygen (oxidant), particles are highly reactive and can ignite system walls more actively and at higher temperatures.
Oxidation based thermal effects are responsible of mechanical properties lost leading to the destruction of the pressure equipment wall.
To deal with this problem, a numerical analysis is done regarding a sample representative of a wall subjected to pressure and temperature. The validation and analysis is done comparing the numerical simulations results to experimental measurements.
More precisely, in this work, we propose a numerical model that describes the thermomechanical behavior of thin metal disks under pressure and subjected to laser heating.
This model takes into account the geometric and material nonlinearity and has been validated by the comparison of simulation results with experimental measurements.
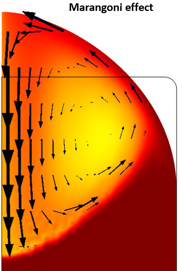