Thin Microchip Release From a Carrier Tape: Structural Mechanics and Vacuum Forces
During semiconductor manufacturing, finished silicon microchips need to be released from a carrier tape they stick to by an adhesive. This is done by vacuum forces that (a) hold the chip flat from above and (b) pull the tape off from the chip underside. Sounds simple, but is very tricky because the material is thin and brittle. When the chip thickness recently reached 20 micrometer, it became clear that the stabilizing vacuum force from above will get more and more important. Previous simulations of the release process using the COMSOL Multiphysics® Structural Mechanics module did not yet include this force [1].
In this paper I will present first results of an attempt to simulate both vacuum forces by COMSOL Multiphysics®: (a) Forces that hold the chip flat from above are produced by a rubber gripper tool with vacuum channels. (b) Forces that pull the tape from below are generated by sucking down the carrier tape onto a platform with moving mechanical parts. When holding the chip with a rubber gripper, two states are possible: either the chip edge is bent down giving rise to vacuum leakage, or it is flat and seals the gripper tool. So far I was not able to handle both states with the Fluid-structure interaction multiphysics coupling since this feature does not support topological changes (e.g. a collapsing mesh).
Therefore I am using a different approach by combining two separate models: (a) A first model calculates vacuum forces from above for a range of pre-defined chip bendings, as shown in the figure. A second model (b) is based on previous simulations [1] including only vacuum forces from below. Here the dynamics of tape release is calculated step by step using the result of one step to update the geometry of the next step. What has been added now is to also use the resulting chip bending in one step to define the force pulling the chip upwards in the next step.
The main goal of this simulation is to understand how chip bending stress during tape release can be reduced by geometric, temporal and material parameters. Results that will be presented:
- Optimization of rubber gripper tool geometry, already in use at our customer
- Impact of carrier tape adhesion, based on data from a tape supplier we collborate with
- Impact of process speed and sequence
- Understanding the physics of the critical first milliseconds of tape release
References
[1] “Peeling Away Memory Chips”, edited by Lexi Carver, Comsol Multiphysics Simulation: An IEEE Spectrum Insert 2017, page 19
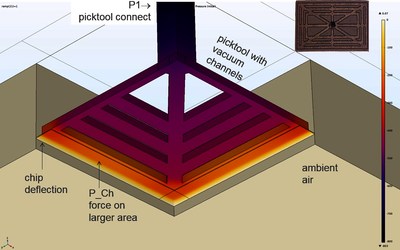