Ultrasonic Power Delivery Through a Steel Wall - Water Interface
This simulation study analyzed ultrasonic power delivery by low-frequency (20-50 kHz) high-power ultrasonic actuation into fluid through a steel wall.
The Acoustic-Piezoelectric Interaction, Frequency Domain interface of the COMSOL Acoustics Module were employed for this study. The wall was modeled by a 5 mm thick circular steel plate and the fluid medium by a water semi sphere, the external surfaces of which featured perfectly matched layers so as to represent an infinite plate on top of a semi-infinite fluid half-space (see figure). A high-power ultrasonic piezoelectric stack transducer actuated the wall at a 20 kHz frequency. Effects of the transducer head diameter (38-90 mm) on acoustic power transmission and sound directivity were evaluated. Acoustic power transmission was quantified as the ratio of ultrasonic power delivered into the fluid to the power delivered to the plate (Lamb waves). The delivered powers were in both cases determined by surface integrals of acoustic intensities at the respective PML boundaries.
Increasing the head diameter increased power transmission and directivity. A narrow transducer head (Ø=40 mm) worked almost like a spherical radiator featuring oblique wave vectors with respect to the plate. Oblique wave vectors tend to reflect at the plate-fluid interface, thus creating Lamb waves. Consequently the power delivery ratio (-2 dB) and directivity index (1 dB) were low. Increasing the head diameter (up to at least 90 mm) increased the relative amount of wave vectors perpendicular to the plate and the head acted like a plane wave radiator. As a result, the power delivery ratio (2.5 dB) and directivity index (14 dB) were improved. On the other hand, while the 90 mm head approaches a half wavelength (~120 mm), the head features a displacement profile with respect to the radial distance which limited the relative benefit of increasing the head diameter.
These simulations predict that adjusting the ultrasonic radiator diameter could significantly increase power delivery in low-frequency high-power ultrasonic applications, such as ultrasonic cleaning or processing in containers that feature thick-walls.
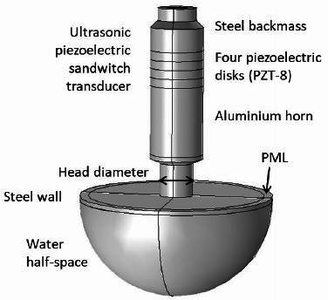
Download
- moilanen_poster.pdf - 0.43MB
- moilanen_abstract.pdf - 0.1MB