Force and Torque Predictions in a Large-Gap Magnetic Suspension System
Magnetic Suspension and Balance Systems (MSBS) are a method of levitating an aerodynamic model in a wind tunnel. An unusual characteristic is that the electromagnet assemblies (outside the wind tunnel) are very large, but the levitated object (a permanent magnet core) is quite small and is located some distance from the electromagnets. Accurate predictions of forces and moments on the levitated core are a critical part of the design process, also for development of model-based feedback control systems. Forces arise from field gradients, torques from quasi-uniform fields. Traditionally, these calculations rely on evaluation of applied fields at the model centroid. A more general approach is integration of the Maxwell stress tensor over suitable surfaces. The latter approach has issues with sharp peaks in stress at corners and edges, although this can be alleviated by using control surfaces located away from material boundaries. Both approaches require certain assumptions related to the material properties of the permanent magnet. This paper compares results from both techniques and makes recommendations for best procedures, with experimental verification planned. Figure 1 shows a typical MSBS in operation and Figure 2 an example of magnetic flux density and Maxwell stress over the surface of a cylindrical core. An additional challenge is accurate prediction of the fields form the electromagnet array itself. These are water-cooled, hollow-conductor electromagnets, some with laminated iron cores, and exhibit a somewhat unusual configuration in the example under study. Fields are calculated on a 3D grid of points, with gradients recovered by surface fitting. Experimental verification by gaussmeter surveys in the useful region of the test section is planned. All calculations discussed are carried out in 3D, using the AC/DC Module, Electrostatics interface.
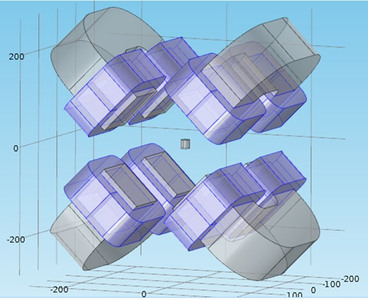