Hydrodynamic Modeling of a Rotating Cone Pump Using COMSOL Multiphysics® Software
Introduction Velocity profiles in liquid films flowing over rotating conical surfaces are of considerable interest in industry. The efficiency of important process equipment, such as spinning cone columns, fluid degassers, centrifugal disc atomizers, centrifugal film evaporators, and rotating packed bed reactors, is greatly influenced by the nature of the fluid velocity distributions. Conical pumps offer simple alternatives to conventional pumps yet the analysis of pump performance has received minimal attention in the literature. Robust models that allow prediction of pump performance would be useful for guiding new designs for various applications versus using less efficient empirical approaches.
Use of COMSOL Multiphysics® software: COMSOL Multiphysics® software provides a powerful modeling platform for modeling of complex fluid dynamic systems, such as rotating cone pumps. The emphasis of this paper is to develop a realistic model for fluid transport based on the 3-D transient Navier-Stokes equations for an assumed geometry (Fig. 1) using COMSOL Multiphysics® software. Unsteady incompressible fluid flow in the annular region of a rotating cone is analyzed under both laminar and turbulent flow conditions. No slip boundary conditions were applied at the solid walls. Both the inner cone and the fluid are rotating about the axis of the cone with time-dependent angular velocities. Results/Conclusions: Numerical simulations have been performed to determine fluid velocity and pressure profiles throughout the system for various geometrical parameters and process conditions. The combined effects of angular rotational speed (Ω), cone height (H), and the ratio of outer to inner radius (κ) on the volumetric flowrate (Q) have been systematically studied. Initial simulation results acquired from laminar flow model (Fig.2) revealed an excessive transport and pumping capacity of the rotating cone, even with small cone sizes. Fluid flow rates of 0.3 to 0.8 L/s were achieved for a design having an inner diameter as low as 10 cm. For increasing values of Ω, the volumetric flowrate was found to be increasing proportionally and was independent of height of the cone (H) and the aspect ratio (κ). Fluctuations in volumetric flowrate were more evident at higher rotational speeds, but were less significant upon increase in cone height. Comparison for different flow regimes has been carried out and results for the same will be presented.
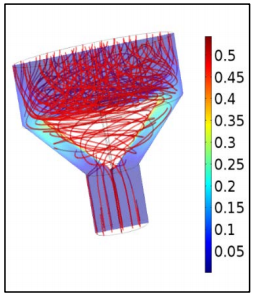
Download
- nagaraj_presentation.pdf - 0.85MB
- nagaraj_poster.pdf - 1.72MB
- nagaraj_paper.pdf - 0.39MB
- nagaraj_abstract.pdf - 0.12MB