Numerical Modeling of Wire Directed Energy Deposition Additive Manufacturing (Wire-DED) Process
COMSOL Multiphysics® is being utilized to develop Thermal Model for Wire Directed Energy Deposition Additive Manufacturing (Wire-DED) process with an objective to analyse the heat transfer phenomenon during and after the process. Wire-DED process’s growing industrial acceptance at a very fast pace has led to a great interest in both scientific and industrial world for the better understanding of the physical phenomenon of the process. Numerical Simulation can be an important tool to develop the better understanding of Wire-DED process. Therefore, a Thermal Model coupled with different Numerical Material Addition strategies is developed in COMSOL Multiphysics®. Numerical Heat Source along with Material Addition Model is required to represent input arc energy and deposited wire respectively in Wire-DED process. A 3-D parametrised volumetric heat source is used to represent input laser energy along with programmed trajectory and Material Activation is used to represent material addition. Heat Transfer in Solids interface is used to implement Numerical Heat Source and perform the heat transfer analysis and Structural Mechanics Module is used to utilize the Activation feature so as to model Numerical Material Addition. Considering experiment results obtained from literature for fabrication of build walls, at first developed Thermal Model with different Numerical Material addition strategies is compared in terms of accuracy and computation time. At last, an efficient Numerical Material Addition Model is developed and proposed that can further reduce the computation cost without losing the computation accuracy.
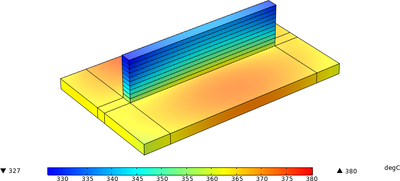
Download
- V_Nain-Comsol_North-America_VN.pdf - 2.89MB