Numerical simulation of a magnetic refrigerator with an improved valve-system design
Vapor-compression technology has been the dominant refrigeration technology for decades, due to its scalability, relatively compact size, high reliability, and other attributes. However, the refrigerants used in vapor-compression equipment have detrimental effects on the global environment when released into the atmosphere. Magnetic refrigeration technology is becoming a promising alternative to conventional refrigeration owning to the advantages of environmental friendliness,high potential efficiency,low noise and vibration. As a kind of solid-state refrigeration technology, magnetic refrigeration is based on the magnetocaloric effect (MCE). MCE is a magneto-thermodynamic phenomenon in which a temperature change of a material is caused by exposing the material to a changing magnetic field. For most magnetocaloric materials, at a moderate magnetic field (1.5T), the adiabatic temperature change is limited to maximum 5 K. This value is not sufficient for practical cooling applications. To enlarge the temperature span, active magnetic regenerator (AMR) is used in current magnetic refrigerators. Meanwhile,multiple regenerator beds is also used to increase the cooling power. To realize active magnetic regeneration and to control the fluid flow in different regenerator beds, oscillating flow and a valve system are required. But this may cause two issues. One is the so-called dead volume, which means the volume between the AMR and the heat exchangers. Due to the oscillating flow, the dead volume would make the fluid to remain in it and consequentially impede heat transfer. The other one is the heat leak from the switching of valves. The heat generally generates by eddy current for solenoid valves or friction for mechanical valves. In this paper, we use COMSOL software to improve the refrigerator design to solve the problems above. To reduce the dead volume,the check valves are installed on the connecting pipes between AMR and heat exchangers to make a unidirectional. The solenoid valves are installed at the hot end of the AMR to avoid the eddy-current heat leaking to the cold exchanger directly. A two-dimensional and transient model is established and the MCE is modeled. The fluid flow is governed by the Navier-Stokes equations and the energy equation governs heat transfer inside solid and fluid. The MCE is taken into account by the inclusion of a source term in the energy equation. The porous media interface and local non-equilibrium module are used to describe the flow and heat transfer in AMR. Compared with other numerical software, COMSOL Multiphysics is more flexible in modifying the underlying equations, hence the flow constraints are added at the inlets and outlet, instead of moving mesh, to simulate the switching of the valves. This can effectively reduce the amount of calculation. The simulation results have proved such a design can reduce the adverse impact of dead volume and heat leak from valves on the cooling performance.
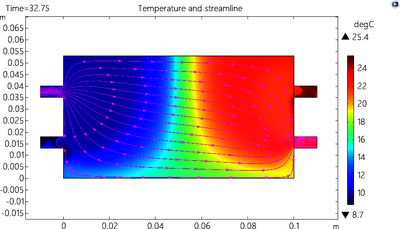
Download
- 李_poster.pdf - 0.53MB
- 李_abstract.pdf - 0.02MB