Phase Transformation and Deformation Model for Quenching Simulations
Heat treatment of the advanced steel grades (like micro-alloyed steels or AHSS steel grades) is a challenging process as the residual stress/deformation are very pronounced and the customer quality requirements are getting stricter. Instead of a trial and error based process control, a model based optimal process control is essential to reduce waste material costs and to stay competitive.
A comprehensive COMSOL® model was developed to simulate the complex heat treatment phenomena to estimate the residual stresses and deformation as an initial step. The model consists of strongly coupled physics of heat transfer, micro-structure change, and deformation fields. The major couplings are: the latent heat of phase transformation, the volume change (due to temperature and micro-structure change), and transformation induced plasticity (trip). Moreover, the nonlinearities like: creep, large deformation and buckling are included as well.
The constitutive model parameters as well as the isothermal and martensitic transformation kinetic parameters are calibrated and validated by dilatometry tests for a certain type of steel.
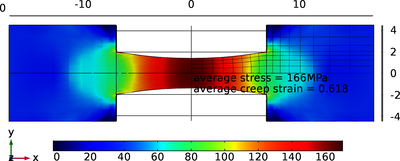
Download
- kaymak_presentation.pdf - 1.43MB
- kaymak_poster.pdf - 1.85MB
- kaymak_paper.pdf - 1.16MB
- kaymak_abstract.pdf - 0.04MB