Reassessing Electrothermal Simulation Techniques to Develop Realistic Models
Electrokinetic (EK) techniques have been broadly implemented in a variety of fields, including microfluidics and lab-on-a-chip, and are seeing increased interest to miniaturize and optimize fluid pumping and mixing systems. While EK techniques such as electro-osmosis and dielectrophoresis have seen applications in limited application areas, particle sorting, and fluid mixing, AC Electrothermal (ACET) is a technique that has seen adoption in microfluidic pumping systems with high conductivity (> 0.2 S/m) fluids, such as biofluids and pharmaceuticals. ACET pumping is well suited to high conductivity fluids as Joule heating is the primary driving force, which is directly proportional to fluid conductivity [1]. Additionally, the presence of an electric double layer is not required, as in other EK techniques, which would necessitate lower conductivity fluids. COMSOL Multiphysics® is traditionally used as a modelling tool for ACET phenomena, due to the multiphysics nature of the systems, incorporating AC/DC, Heat Transfer, and Fluid Flow Modules. This paper addresses the range of simplifications and assumptions made to reduce computational times and model complexity in existing work in the field and provides suggestions to improve models to better reflect real world observations . This involves the addition of the electromagnetic heating multiphysics module to incorporate joule heating in a more cohesive manner. Traditionally, ACET devices consist of ‘units’ comprised of a small and large electrode (~100nm height) on the base of a channel (~200um height), in which an AC signal is applied to the small electrode, and the large electrode is designated as ground. These electrode ‘units’ are repeated anywhere from 2 to 4000 pairs to generate flow. Most reported simulations in this area typically rely on 2D simulations, effective DC voltages, planar electrodes, and bypass channel wall behaviours to simplify the system to save on computational resources, [1]–[3]. This work addresses many of these factors and their individual and collective impacts on ACET modelling and flow rate accuracy. Our work shows significant discrepancies between flow rates under the simplification assumptions and our proposed, more realistic, model. Using modern enhanced computing tools, the results outlined in this work will allow for ACET and broader EK modelling to more closely resemble real devices and improve simulation accuracy to produce more meaningful theoretical results. This allows for model analysis and improvement with certainty that simulation changes reflect manufactured system outcomes. This will lead to better understanding and uptake of the technique.
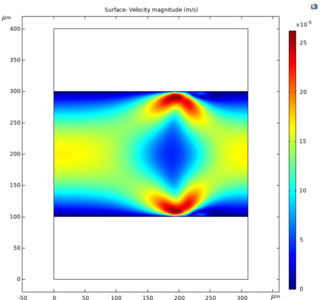