Remote Monitoring of Structures in Composite Materials via Embedded Thermo-Chemical Sensors
Composite systems are becoming more and more widespread across industries and the capability to finding and tracking internal defects before they have grown to major deterioration is of paramount importance in regard to safety, economy and maintenance. We are exploring a novel method of internal damage detection and tracking in composite material using thermo-chemical sensing. Various types of composite materials with this structural health monitoring technology embedded are investigated computationally by implementing COMSOL Multiphysics® software. The RF module is capable of Electromagnetic Heating simulation and the analysis results can be used as inputs for Heat Transfer Module to evaluate the temperature of the Material's surface at any point and any time. Microwave Oven from the Application Library was used as an example to get started with the simulation in this study. This paper sheds light on the physics enabling detection and monitoring, including the microwave heating and subsequent cooling of the composites material, and undertakes a sensitivity study of the technology. The specimen is modeled in COMSOL® to study the sensing methodology particularly for the purpose of feasibility and optimization. In regard to the required physics of the model: Two different physics are coupled in the computation, electromagnetic heating and heat transfer. One challenge prior to running the analysis is certainly to define the input parameters required to run a successful simulation, specifically, dielectric constant, electrical conductivity and thermal conductivity. Several test parameters, such as the polar medium volume and the composite layup has been varied in this study. It is noticed that the 0.2ml polar product volume results in a stronger temperature signal than the 0.1ml volume. Further, the 6-layer layup reduces the thermal signal being sensed on the composite surface compared to the 2-layer layup. The method is able to clearly represent the damage location, size and growth rate in macro-scale.
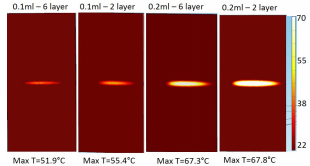
Download
- golchinfar_presentation.pdf - 2.01MB
- golchinfar_abstract.pdf - 0.07MB