COMSOL Events Calendar
Modeling Workflow
Electromagnetics
Structural & Acoustics
Fluid & Heat
Chemical
Interfacing
General
Show as:
Time zone:
My Time (EDT)
Host Time
08:00 AM - 08:00 PM
Showing events starting between: 8 a.m. – 8 p.m.
Search
Upcoming Events
Loading Events
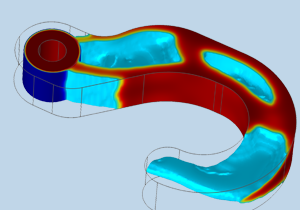
May 13
| 8:00 a.m. BST
Optimierung keramischer 3D-Drucke durch Simulation
COMSOL
Webinar
Online
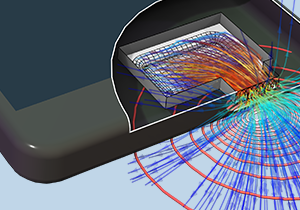
May 14
| 8:30 a.m. CEST
Analizzare i fenomeni acustici con la simulazione
COMSOL
Webinar
Online
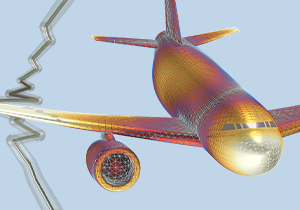
May 20
| 8:00 a.m. CEST
Modeling for Aerospace Engineering with COMSOL Multiphysics®
COMSOL
Webinar
Online
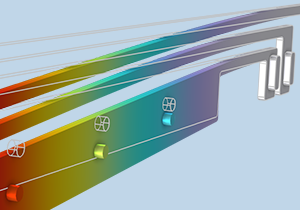
May 20–23
| 11:00 a.m. EDT
Introduction to COMSOL Multiphysics®
COMSOL
Training Course
Online

May 20
| 2:00 p.m. EDT
Acoustics in Electronics Series, Part 4: Piezoelectric Devices
COMSOL
Webinar
Online

May 22
| 2:00 p.m. EDT
Optimizing Wireless Power Transfer Systems Through Simulation
IEEE
Webinar
Online
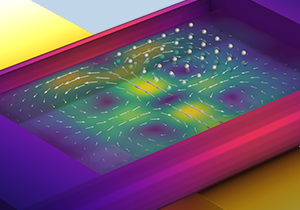
May 27–30
| 11:00 a.m. EDT
Acoustics Modeling in COMSOL Multiphysics®
COMSOL
Training Course
Online
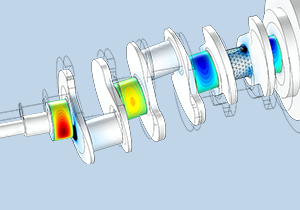
May 28
| 9:00 a.m. BST
Introduction to Multibody Dynamics Modeling with COMSOL Multiphysics
COMSOL
Webinar
Online

May 29
| 11:00 a.m. EDT
COMSOL Day: Semiconductor Processing & Packaging
COMSOL
COMSOL Day
Online
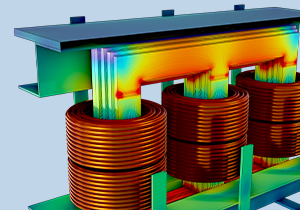
Jun 3
| 8:00 a.m. CEST
Electromagnetics Modeling with COMSOL® in 18 Minutes
COMSOL
Webinar
Online

Jun 4
| 8:30 a.m. CEST
Migliorare le tecnologie per la decarbonizzazione con la simulazione
COMSOL
Webinar
Online

Jun 10
| 10:40 a.m. EDT
Battery Modeling with COMSOL Multiphysics®
Teach Briefs
Webinar
Online

Jun 12
| 9:00 a.m. BST
Optimization in Structural Mechanics
COMSOL
Webinar
Online
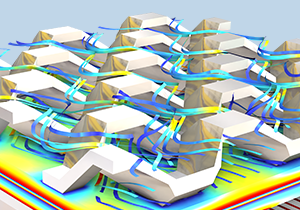
Jun 12
| 9:00 a.m. BST
Hydrogen Technology Innovation with Simulation
The Engineer
Webinar
Online

Jun 12
| 2:00 p.m. EDT
Underwater Acoustics
COMSOL
Webinar
Online

Jun 17
| 8:00 a.m. CEST
Battery Design and Thermal Management
COMSOL
Webinar
Online

Jun 24–27
| 11:00 a.m. EDT
Introduction to COMSOL Multiphysics®
COMSOL
Training Course
Online
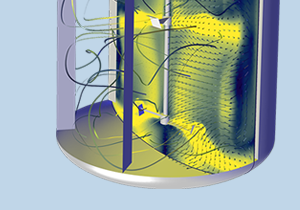
Jun 26
| 2:00 p.m. EDT
Modeling Fluid Mixers and Stirred Tank Reactors in COMSOL Multiphysics®
COMSOL
Webinar
Online
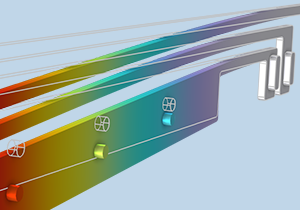
Jul 22–25
| 11:00 a.m. EDT
Introduction to COMSOL Multiphysics®
COMSOL
Training Course
Online
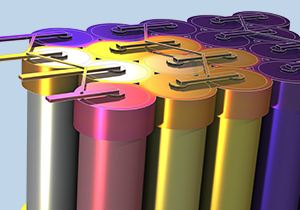
Aug 5–8
| 11:00 a.m. EDT
Battery Modeling in COMSOL Multiphysics®
COMSOL
Training Course
Online

Aug 26–29
| 11:00 a.m. EDT
AC/DC Modeling in COMSOL Multiphysics®
COMSOL
Training Course
Online
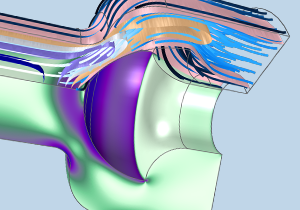
Sep 9–12
| 11:00 a.m. EDT
CFD Modeling in COMSOL Multiphysics®
COMSOL
Training Course
Online
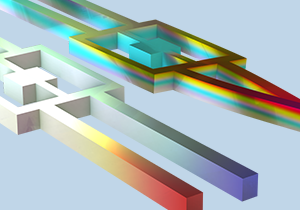
Sep 16–19
| 11:00 a.m. EDT
Structural Mechanics Modeling in COMSOL Multiphysics®
COMSOL
Training Course
Online
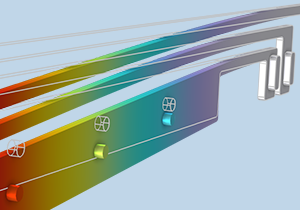
Sep 23–26
| 11:00 a.m. EDT
Introduction to COMSOL COMSOL Multiphysics®
COMSOL
Training Course
Online
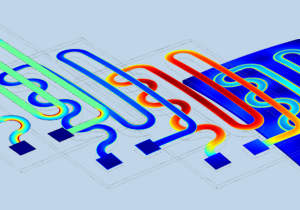
Oct 14–17
| 11:00 a.m. EDT
Heat Transfer Modeling in COMSOL Multiphysics®
COMSOL
Training Course
Online

Oct 21–24
| 11:00 a.m. EDT
RF Modeling in COMSOL Multiphysics®
COMSOL
Training Course
Online
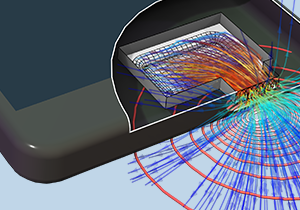
Oct 28–31
| 11:00 a.m. EDT
Acoustics Modeling in COMSOL Multiphysics®
COMSOL
Training Course
Online
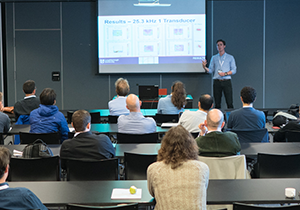
Nov 4–5
| 9:00 a.m. EDT
Introduction to COMSOL Multiphysics®
COMSOL
Training Course
Burlington

Nov 11–14
| 11:00 a.m. EDT
Electrochemistry & Electrodeposition Modeling in COMSOL Multiphysics®
COMSOL
Training Course
Online
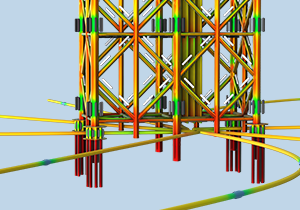
Nov 18–20
| 11:00 a.m. EDT
Corrosion Modeling in COMSOL Multiphysics®
COMSOL
Training Course
Online
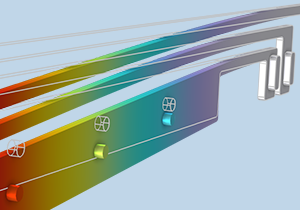
Dec 9–12
| 11:00 a.m. EDT
Introduction to COMSOL Multiphysics®
COMSOL
Training Course
Online
Showing 8 of 31 events
Showing 31 of 31 events
Date | Time | Title | Type | Host | Discipline |
---|---|---|---|---|---|
May 13 | 8:00 a.m. |
Optimierung keramischer 3D-Drucke durch Simulation |
Webinar | COMSOL-Online |
|
May 14 | 8:30 a.m. |
Analizzare i fenomeni acustici con la simulazione |
Webinar | COMSOL-Online |
|
May 20 | 8:00 a.m. |
Modeling for Aerospace Engineering with COMSOL Multiphysics® |
Webinar | COMSOL-Online |
|
May 20–23 | 11:00 a.m. |
Introduction to COMSOL Multiphysics® |
Training Course | COMSOL-Online |
|
May 20 | 2:00 p.m. |
Acoustics in Electronics Series, Part 4: Piezoelectric Devices |
Webinar | COMSOL-Online |
|
May 22 | 2:00 p.m. |
Optimizing Wireless Power Transfer Systems Through Simulation |
Webinar | IEEE - Online |
|
May 27–30 | 11:00 a.m. |
Acoustics Modeling in COMSOL Multiphysics® |
Training Course | COMSOL-Online |
|
May 28 | 9:00 a.m. |
Introduction to Multibody Dynamics Modeling with COMSOL Multiphysics |
Webinar | COMSOL-Online |
|
May 29 | 11:00 a.m. |
COMSOL Day: Semiconductor Processing & Packaging |
COMSOL Day | COMSOL-Online |
|
Jun 3 | 8:00 a.m. |
Electromagnetics Modeling with COMSOL® in 18 Minutes |
Webinar | COMSOL-Online |
|
Jun 4 | 8:30 a.m. |
Migliorare le tecnologie per la decarbonizzazione con la simulazione |
Webinar | COMSOL-Online |
|
Jun 10 | 10:40 a.m. |
Battery Modeling with COMSOL Multiphysics® |
Webinar | Teach Briefs - Online |
|
Jun 12 | 9:00 a.m. |
Optimization in Structural Mechanics |
Webinar | COMSOL-Online |
|
Jun 12 | 9:00 a.m. |
Hydrogen Technology Innovation with Simulation |
Webinar | The Engineer - Online |
|
Jun 12 | 2:00 p.m. |
Underwater Acoustics |
Webinar | COMSOL-Online |
|
Jun 17 | 8:00 a.m. |
Battery Design and Thermal Management |
Webinar | COMSOL-Online |
|
Jun 24–27 | 11:00 a.m. |
Introduction to COMSOL Multiphysics® |
Training Course | COMSOL-Online |
|
Jun 26 | 2:00 p.m. |
Modeling Fluid Mixers and Stirred Tank Reactors in COMSOL Multiphysics® |
Webinar | COMSOL-Online |
|
Jul 22–25 | 11:00 a.m. |
Introduction to COMSOL Multiphysics® |
Training Course | COMSOL-Online |
|
Aug 5–8 | 11:00 a.m. |
Battery Modeling in COMSOL Multiphysics® |
Training Course | COMSOL-Online |
|
Aug 26–29 | 11:00 a.m. |
AC/DC Modeling in COMSOL Multiphysics® |
Training Course | COMSOL-Online |
|
Sep 9–12 | 11:00 a.m. |
CFD Modeling in COMSOL Multiphysics® |
Training Course | COMSOL-Online |
|
Sep 16–19 | 11:00 a.m. |
Structural Mechanics Modeling in COMSOL Multiphysics® |
Training Course | COMSOL-Online |
|
Sep 23–26 | 11:00 a.m. |
Introduction to COMSOL COMSOL Multiphysics® |
Training Course | COMSOL-Online |
|
Oct 14–17 | 11:00 a.m. |
Heat Transfer Modeling in COMSOL Multiphysics® |
Training Course | COMSOL-Online |
|
Oct 21–24 | 11:00 a.m. |
RF Modeling in COMSOL Multiphysics® |
Training Course | COMSOL-Online |
|
Oct 28–31 | 11:00 a.m. |
Acoustics Modeling in COMSOL Multiphysics® |
Training Course | COMSOL-Online |
|
Nov 4–5 | 9:00 a.m. |
Introduction to COMSOL Multiphysics® |
Training Course | COMSOL-Burlington |
|
Nov 11–14 | 11:00 a.m. |
Electrochemistry & Electrodeposition Modeling in COMSOL Multiphysics® |
Training Course | COMSOL-Online |
|
Nov 18–20 | 11:00 a.m. |
Corrosion Modeling in COMSOL Multiphysics® |
Training Course | COMSOL-Online |
|
Dec 9–12 | 11:00 a.m. |
Introduction to COMSOL Multiphysics® |
Training Course | COMSOL-Online |
|
Trainings by Certified Consultants
On-Demand Webinars

Demokratisierung der Multiphysik-Simulation
Webinar
May 08

Acoustics in Electronics Series, Part 3: Hearing Aids
Webinar
May 06

(Online) Introduction to COMSOL Multiphysics® (3 Days)
Training Course
May 06

Comment utiliser le solveur temporel de COMSOL Multiphysics®
Webinar
Apr 24

将随频率变化的数据融入 COMSOL® 时域声学仿真
Webinar
Apr 24
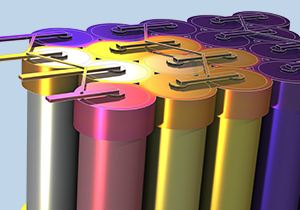
Modéliser les Batteries avec COMSOL Multiphysics®
Webinar
Apr 17
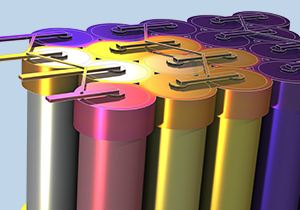
COMSOL® 中的电池仿真
Webinar
Apr 17

Acoustics in Electronics Webinar Series, Part 2: MEMS Speakers and Microphones
Webinar
Apr 16

The Basics of COMSOL Multiphysics® in 18 Minutes
Webinar
Apr 15

Optimization in RF and Wave Optics
Webinar
Apr 09

Wave & Ray Optics Modeling with COMSOL®
Webinar
Apr 09

Modellare le scariche elettriche
Webinar
Apr 09

Meshing Your Models in COMSOL Multiphysics®
Webinar
Apr 08

Multiphysics Simulation in Semiconductor Packaging
Webinar
Apr 03

使用 COMSOL® 模拟生物传感器和检测设备
Webinar
Mar 27

Acoustics in Electronics Webinar Series, Part 1: Loudspeakers
Webinar
Mar 25
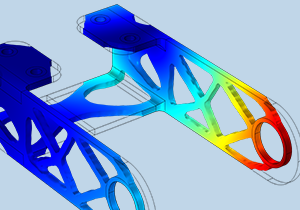
Esperienze di simulazione nell'additive manufacturing: dal design al processo
Webinar
Mar 20
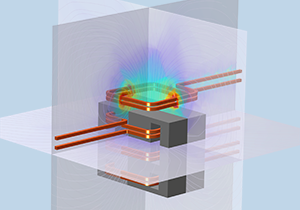
Simulating Electrical Power Systems for the Grid
Webinar
Mar 20
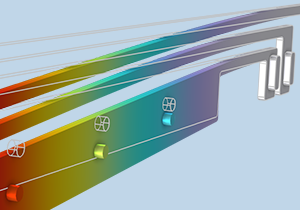
Comment Utiliser Efficacement les Études Stationnaires de COMSOL Multiphysics®
Webinar
Mar 20
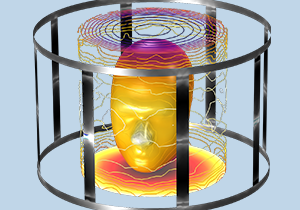
Modellierung biomedizinischer Geräte mit COMSOL Multiphysics®
Webinar
Mar 20
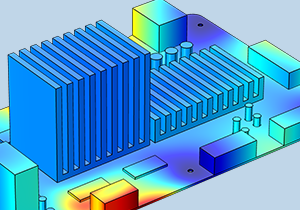
Multiphysics Modeling of Electronic Components
Webinar
Mar 20

使用 COMSOL® 模拟电声器件
Webinar
Mar 20

Using Geometry Modeling Tools in COMSOL Multiphysics®
Webinar
Mar 18

Improving Thermal Management of Batteries with COMSOL Multiphysics®
Webinar
Mar 18

Modéliser les Composants Électroniques avec COMSOL Multiphysics®
Webinar
Mar 13

Modeling Chemical Reactions and Reacting Flows Using COMSOL Multiphysics®
Webinar
Mar 06
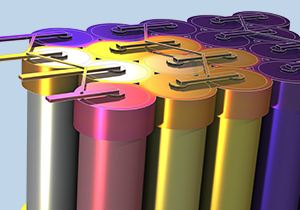
使用 COMSOL® 进行锂离子电池模型的参数估计
Webinar
Mar 06

Integrating Frequency-Dependent Data into Time-Domain Acoustics Analysis
Webinar
Feb 27

使用 COMSOL® 模拟放电现象
Webinar
Feb 27
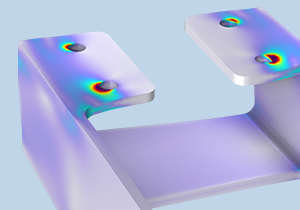
Introduction to Uncertainty Quantification
Webinar
Feb 26
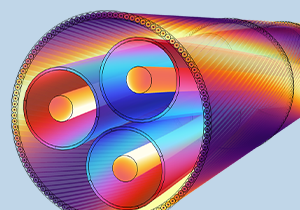
Entwicklung von Leistungselektronik und Kabelsystemen
Webinar
Feb 25
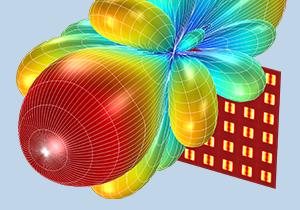
使用 COMSOL® 模拟雷达和天线
Webinar
Feb 20

Efficient Battery Modeling with Surrogate Models
Webinar
Feb 18

Comment construire un maillage dans COMSOL Multiphysics®
Webinar
Feb 18
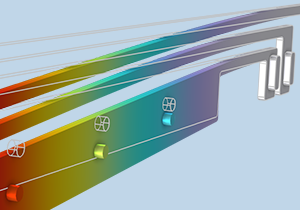
The Basics of COMSOL Multiphysics® in 18 Minutes
Webinar
Feb 13
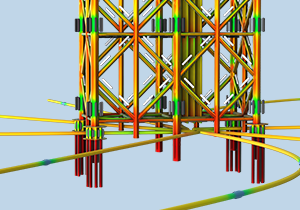
Modéliser la Corrosion et les Systèmes de Protection contre la Corrosion avec COMSOL Multiphysics®
Webinar
Feb 13
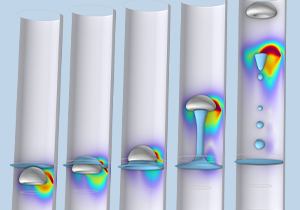
Designing a Magnetorheological-Fluid-Based Clutch Using COMSOL Multiphysics®
Webinar
Feb 13

使用模型管理器进行仿真数据管理
Webinar
Feb 13
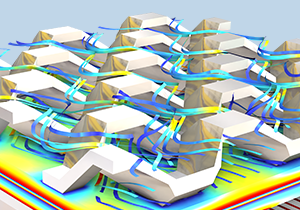
Innovare le tecnologie dell'idrogeno con la simulazione
Webinar
Feb 11
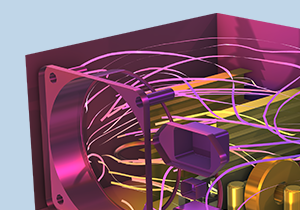
Simulare il comportamento termico di dispositivi e processi
Webinar
Jan 30

Modeling Biochemical Sensors and Testing Devices with COMSOL®
Webinar
Jan 29
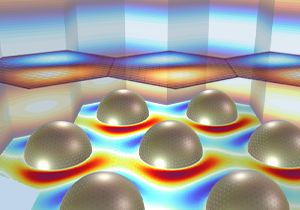
Modeling Optical Nanostructures with COMSOL Multiphysics®
Webinar
Jan 23
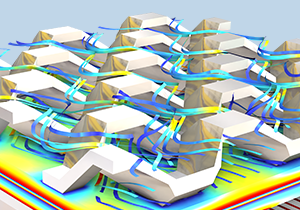
Améliorer les Performances des Piles à Combustible et des Électrolyseurs avec COMSOL Multiphysics®
Webinar
Jan 23

Electric Discharge Modeling
Webinar
Jan 21

Automotive Acoustics Analysis Using COMSOL Multiphysics®
Webinar
Jan 16
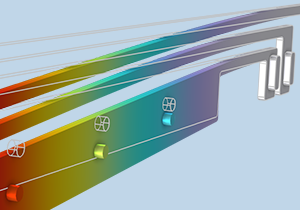
The Basics of COMSOL Multiphysics® in 18 Minutes
Webinar
Jan 14

Comment Construire efficacement sa Géométrie avec le Module Design
Webinar
Jan 14

Tutte le novità di COMSOL Multiphysics® 6.3
Webinar
Jan 10
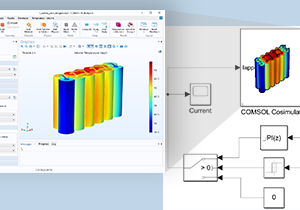
LiveLink™ for MATLAB® 和 LiveLink™ for Simulink® 功能简介
Webinar
Jan 09
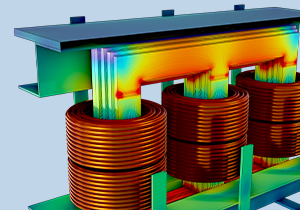
COMSOL® 中的低频电磁场仿真
Webinar
Jan 03
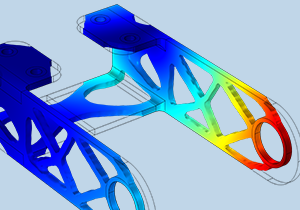
使用 COMSOL Multiphysics® 优化设计
Webinar
Dec 26
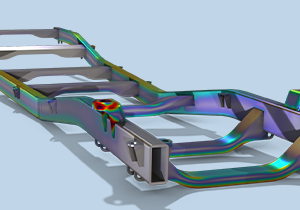
COMSOL® 中的结构力学仿真
Webinar
Dec 19

Multiphysics Fracture Mechanics with COMSOL Multiphysics® in 18 minutes
Webinar
Dec 12
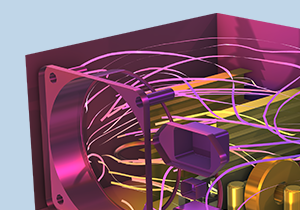
COMSOL® 中的传热仿真
Webinar
Dec 12

Models for Transport and Chemistry in CVD Reactors
Webinar
Dec 05

Modéliser les Procédés de Fabrication avec COMSOL Multiphysics®
Webinar
Dec 05
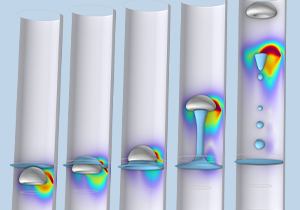
COMSOL® 中的多相流仿真
Webinar
Dec 05

Simulazione elettromagnetica di circuiti stampati (PCB)
Webinar
Dec 04

COMSOL Multiphysics® 6.3 版本功能简介
Webinar
Nov 28

Modeling Nanophotonic Applications with COMSOL Multiphysics®
Webinar
Nov 28

Simulation für alle durch eigenständige Simulations-Apps
Webinar
Nov 27

Design Optimisation for Engineering Problems
Webinar
Nov 27
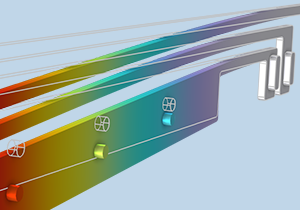
Introducción a COMSOL Multiphysics® en 18 Minutos
Webinar
Nov 26
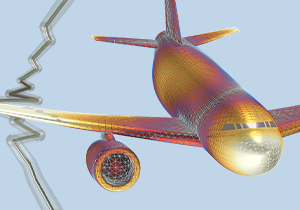
Modélisation Multiphysique pour l’Aéronautique et le Spatial avec COMSOL Multiphysics®
Webinar
Nov 21
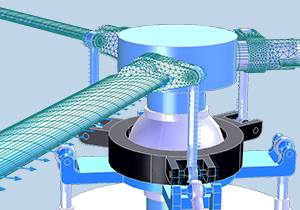
COMSOL® 中的转子动力学和多体动力学仿真
Webinar
Nov 21
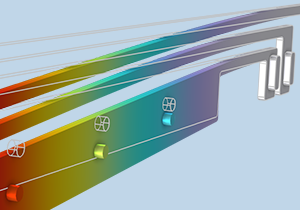
Modeling Shape Memory Alloys and Triboelectric Nanogenerators with COMSOL Multiphysics®
Webinar
Nov 21

Progettare batterie all'avanguardia con la simulazione
Webinar
Nov 20

Introducing COMSOL Multiphysics® Version 6.3
Webinar
Nov 20

Improving Thermal Management of Batteries with COMSOL Multiphysics®
Webinar
Nov 19
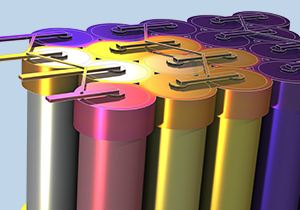
Battery Modeling with COMSOL Multiphysics®
Webinar
Nov 14

Modéliser les Milieux Poreux avec COMSOL Multiphysics®
Webinar
Nov 14

COMSOL® 求解器介绍及设置方法
Webinar
Nov 14
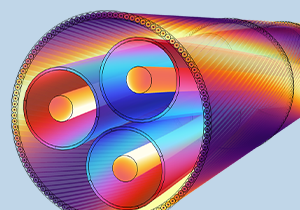
Modeling Cables & Power Electronics
Webinar
Nov 13

Improving the Manufacturing of Semiconductors with Multiphysics Simulation
Webinar
Nov 07
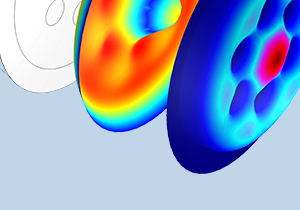
使用 COMSOL Multiphysics® 模拟声学超材料
Webinar
Nov 07
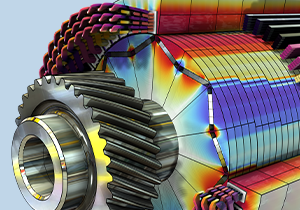
Advancements in Simulation for EV Motors
Webinar
Nov 06
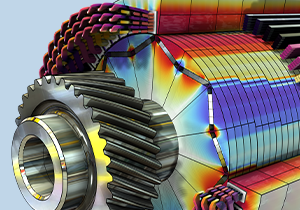
Multiphysics Modeling of Electrical Motors
Webinar
Oct 31
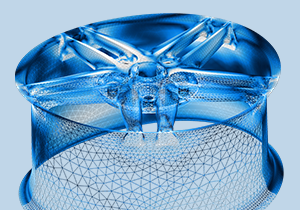
多物理场仿真结果的处理与可视化
Webinar
Oct 24

Modelling the Thermomechanical Behaviour of Glass Materials
Webinar
Oct 23

Fatigue and Durability Analysis using COMSOL Multiphysics®
Webinar
Oct 23
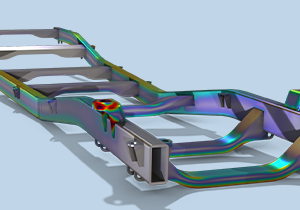
Multiphysics Modeling of Manufacturing Processes Using COMSOL®
Webinar
Oct 17

Déployer les Bénéfices de la Simulation à l’aide d’Applications Autonomes
Webinar
Oct 17
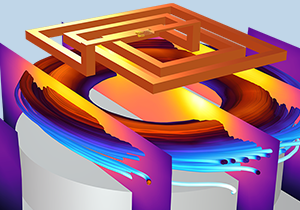
COMSOL® 中的等离子体仿真
Webinar
Oct 17

Simulating Electromagnetic Metamaterials in COMSOL Multiphysics®
Webinar
Oct 15
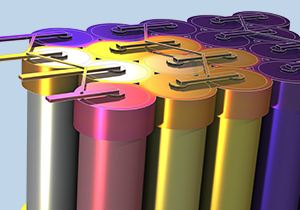
Modeling Thermal Runaway and Abuse in Batteries
Webinar
Oct 15
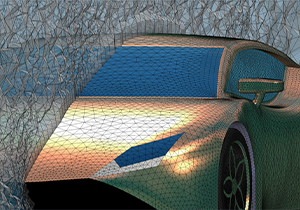
COMSOL® 网格划分功能介绍
Webinar
Oct 10

Simulating Electronics Packaging and Testing
Webinar
Sep 26

Electromagnetics Simulation of Printed Circuit Boards in COMSOL Multiphysics®
Webinar
Sep 26

Simulating Droplet Flow in Wearable Sweat Collection Patches
Webinar
Sep 25
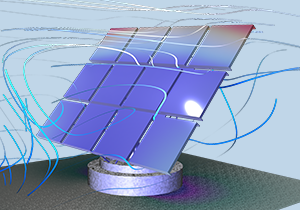
Progettare tecnologie per l'energia solare
Webinar
Sep 24
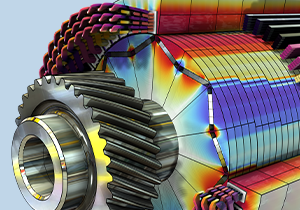
Designing Electric Motors and Drivetrains with Multiphysics Simulation
Webinar
Sep 20
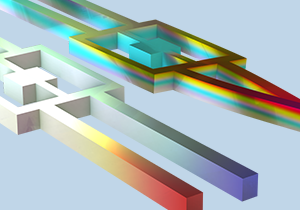
Modeling and Simulation of MEMS Devices
Webinar
Sep 19
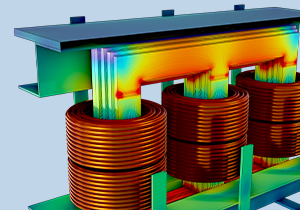
电力变压器的多物理场仿真
Webinar
Sep 19
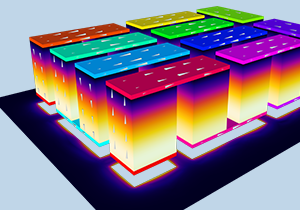
Equation-Based Modeling with COMSOL Multiphysics®
Webinar
Sep 18
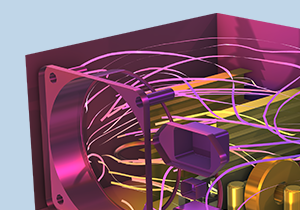
Thermal Management in Electronic Devices with COMSOL Multiphysics®
Webinar
Sep 18

Battery Modeling with COMSOL Multiphysics®
Webinar
Sep 17

Simulation Multiphysique, Modèle de Substitution et Jumeaux Numériques
Webinar
Sep 17
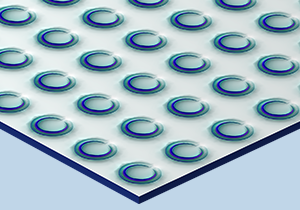
Simulating Plasmonics and Metamaterials
Webinar
Sep 12
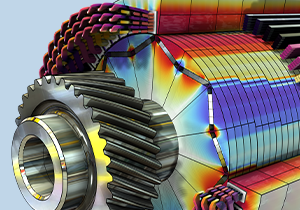
使用 COMSOL Multiphysics® 仿真高性能电机
Webinar
Sep 12
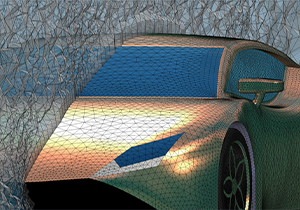
Risolvere modelli di grandi dimensioni con COMSOL Multiphysics®
Webinar
Sep 11
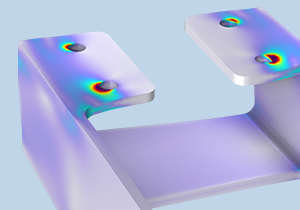
不确定性量化在多物理场仿真中的应用
Webinar
Sep 05
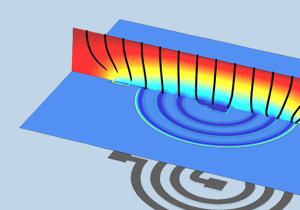
Modeling and Simulation of Electrodeposition Cells
Webinar
Aug 29
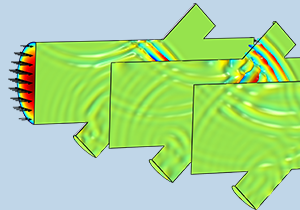
超声波及其应用的多物理场仿真
Webinar
Aug 29
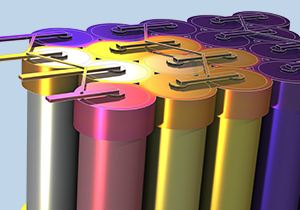
Designing Batteries with Modeling and Simulation
Webinar
Aug 28

Materialparameter abschätzen
Webinar
Aug 28
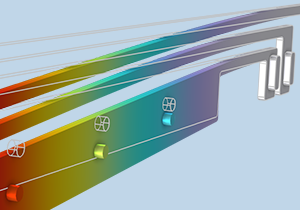
Introducción a COMSOL Multiphysics® en 18 Minutos
Webinar
Aug 27

Multiphysics Modeling and Simulation for 5G Devices
Webinar
Aug 27
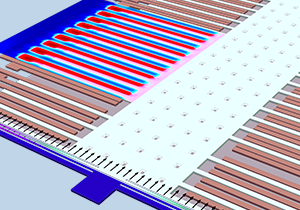
Modeling Low-Frequency Accelerometers Using COMSOL Multiphysics®
Webinar
Aug 22
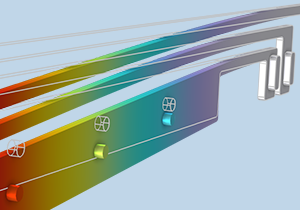
The Basics of COMSOL Multiphysics® in 18 Minutes
Webinar
Aug 20
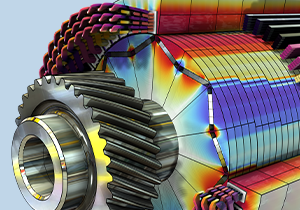
Modeling Electric Motors and Drivetrains
Webinar
Aug 20

Thermal Health Monitoring for the Built Environment: Accelerating Product Development with COMSOL
Webinar
Aug 15
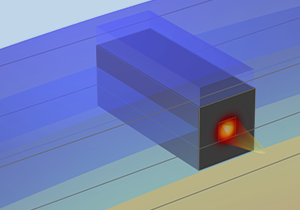
使用 COMSOL Multiphysics® 模拟光电半导体
Webinar
Aug 15

Phased Array Antenna Modeling with COMSOL Multiphysics®
Webinar
Aug 13
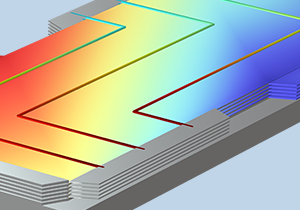
Virtual Hydrogen Lab: Computational Predictions of Hydrogen Uptake, Diffusion, and Embrittlement
Webinar
Aug 08
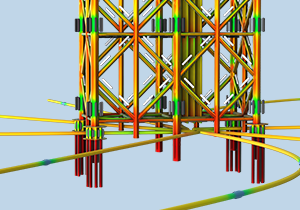
COMSOL® 多物理场仿真加速数字岩心技术发展
Webinar
Aug 08
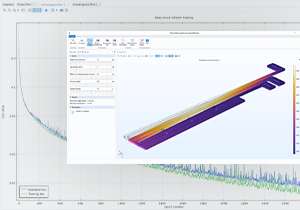
使用代理模型开发高效的 COMSOL® 仿真 App
Webinar
Aug 01

Modeling Fluid-Structure Interaction with COMSOL Multiphysics®
Webinar
Jul 30

Multiphysics Simulation to Improve Design of Renewable Energy Production
Webinar
Jul 25
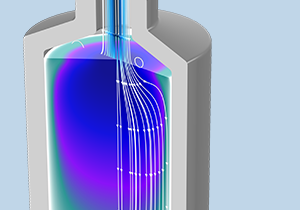
COMSOL® 多物理场仿真在地热能开发中的应用
Webinar
Jul 25
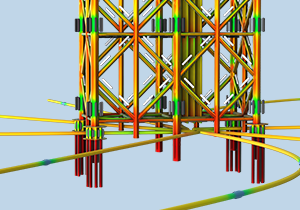
Multiphysics Simulation for Oil & Gas Processing
Webinar
Jul 19

Modeling Hydrogels and Swollen Elastomers in COMSOL Multiphysics®
Webinar
Jul 18
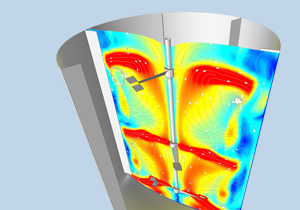
COMSOL® 仿真 App 开发、部署和应用
Webinar
Jul 18
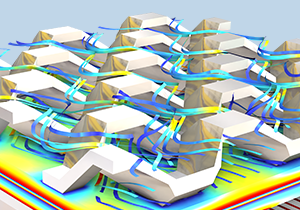
Modeling Hydrogen Fuel Cells and Electrolyzers
Webinar
Jul 17

Modeling Magnetostrictive Material-Based Energy Harvesting Devices
Webinar
Jul 17
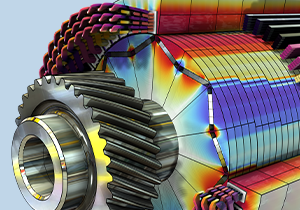
Concevoir des moteurs électriques performants avec COMSOL Multiphysics®
Webinar
Jul 11
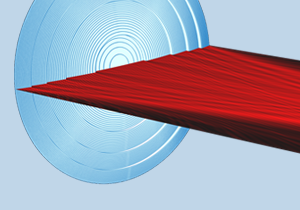
COMSOL® 中的光学仿真
Webinar
Jul 11

I nuovi orizzonti della simulazione acustica
Webinar
Jul 04
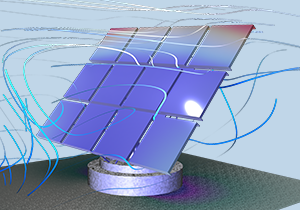
Multiphysics Simulation for Solar Energy Applications
Webinar
Jul 04
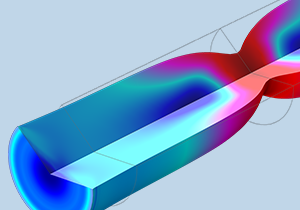
非线性结构材料参数估计
Webinar
Jul 04
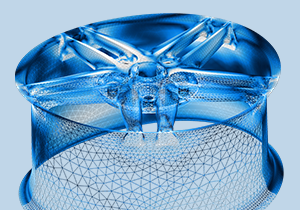
Lightweighting in EVs with Multiphysics Simulation
Webinar
Jun 27
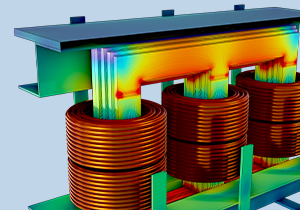
基于 COMSOL® 构建电力设备的数字孪生
Webinar
Jun 27

Optimizing Solar Collectors Using COMSOL Multiphysics®
Webinar
Jun 27
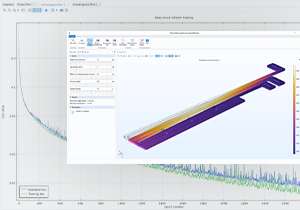
The Democratization of Multiphysics Simulation
Webinar
Jun 26
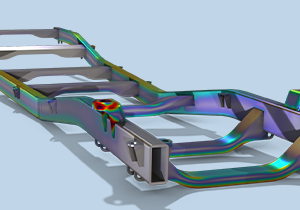
Performing Fatigue and Durability Analysis Using COMSOL Multiphysics®
Webinar
Jun 26
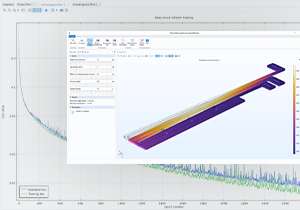
Comment accélérer vos Applications de Simulation avec des Modèles de Substitution
Webinar
Jun 25
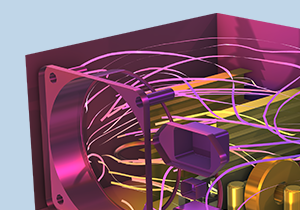
Modéliser les Composants Électroniques avec COMSOL Multiphysics®
Webinar
Jun 20
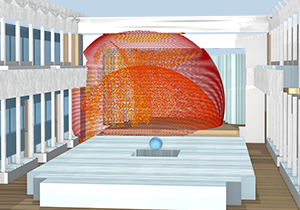
COMSOL® 室内声学仿真
Webinar
Jun 20

Simulare fenomeni termomeccanici
Webinar
Jun 18

Simulating Current-Driven Magnetohydrodynamic Flows Using COMSOL Multiphysics®
Webinar
Jun 18

Thermal Modeling of Lasers in Manufacturing Processes
Webinar
Jun 13

Driving Innovation in EV Battery Design with Multiphysics Simulation Tools
Webinar
Jun 13
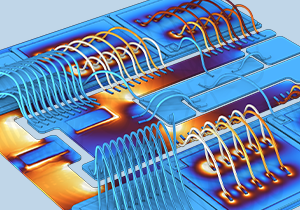
COMSOL Multiphysics® 在半导体制造中的应用
Webinar
Jun 13
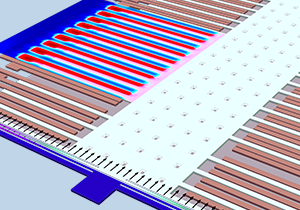
Modeling MEMS Accelerometers Using COMSOL Multiphysics®
Webinar
Jun 06

Multiphysics modelling of photonic devices with COMSOL
Webinar
Jun 06
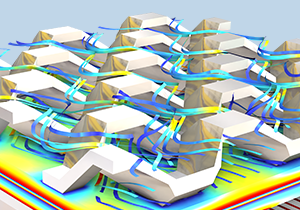
COMSOL Multiphysics® 在绿氢技术中的应用
Webinar
Jun 06
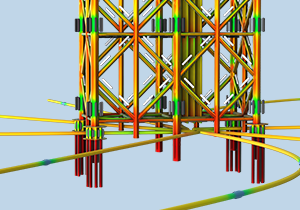
Modeling Corrosion and Corrosion Protection Systems with COMSOL Multiphysics®
Webinar
May 30
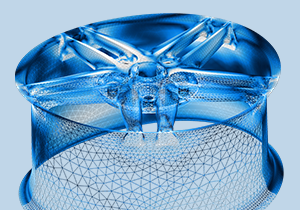
Comment Exploiter efficacement vos Résultats de Simulation avec COMSOL Multiphysics®
Webinar
May 30

Modeling Pharmaceutical Processes with COMSOL Multiphysics®
Webinar
May 29
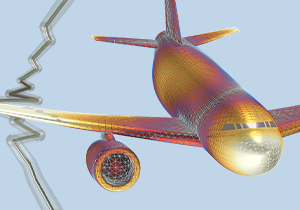
使用 COMSOL Multiphysics® 模拟放电现象
Webinar
May 28

Modéliser les Dispositifs Électroacoustiques avec COMSOL Multiphysics®
Webinar
May 23
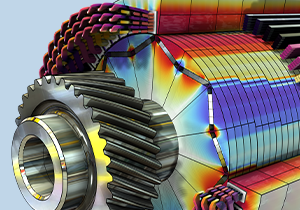
Modeling Electric Motors and Drivetrains
Webinar
May 22
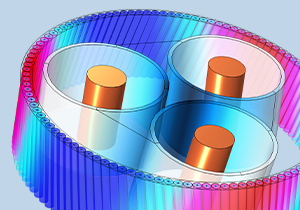
Modeling Cable Design & Power Electronics
Webinar
May 21
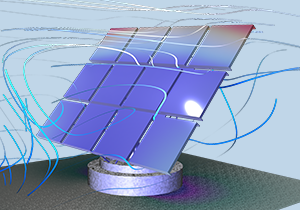
Pioneering Sustainable Solar Technologies with COMSOL Multiphysics®
Webinar
May 21
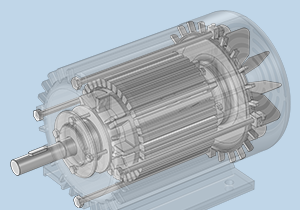
Modellare e gestire geometrie complesse
Webinar
May 16
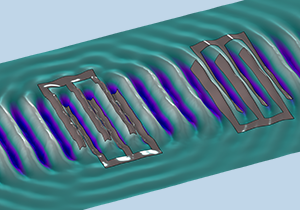
使用 COMSOL® 模拟 SAW/BAW 器件
Webinar
May 16
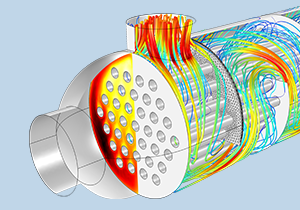
COMSOL® 中的换热器仿真
Webinar
May 09
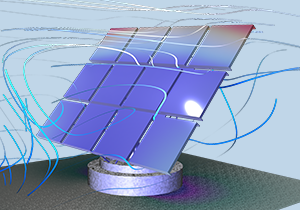
COMSOL Multiphysics® 中的流固耦合仿真
Webinar
Apr 18
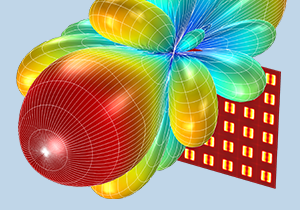
多尺度电磁波仿真
Webinar
Apr 11
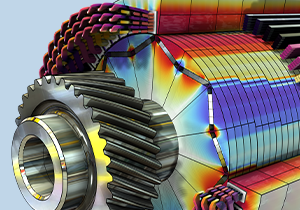
COMSOL® 微执行器和微型电机仿真
Webinar
Apr 02
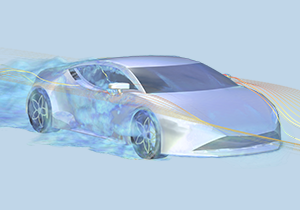
COMSOL® 中的湍流仿真
Webinar
Mar 26
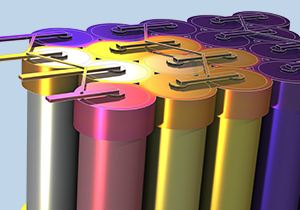
Modeling Thermal Runaway and Abuse in Batteries
Webinar
Mar 21
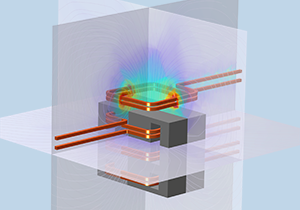
COMSOL® 仿真在电力电子技术中的应用
Webinar
Mar 14
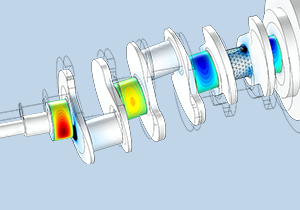
COMSOL® 中的流体动压轴承仿真
Webinar
Mar 12
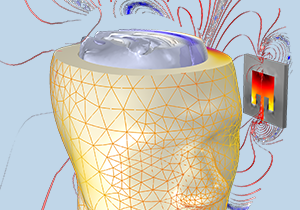
使用 COMSOL Multiphysics® 模拟 EMI/EMC 现象
Webinar
Mar 07
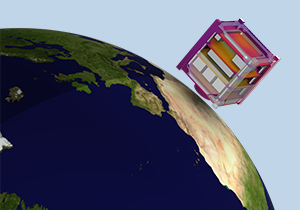
COMSOL® 中的热辐射仿真
Webinar
Mar 05
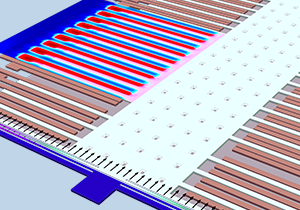
使用 COMSOL Multiphysics® 模拟 MEMS 加速度计和陀螺仪
Webinar
Feb 29
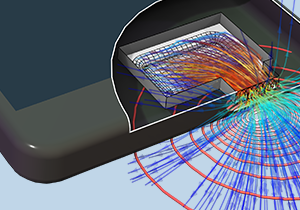
COMSOL® 中的扬声器和麦克风仿真
Webinar
Jan 04
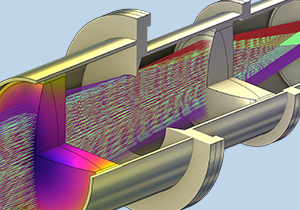
使用 COMSOL Multiphysics® 进行结构-热-光学耦合分析
Webinar
Dec 21
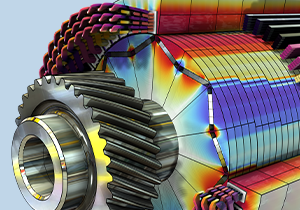
Improving Electric Drivetrain Efficiency with Multiphysics Simulation
Webinar
Dec 15
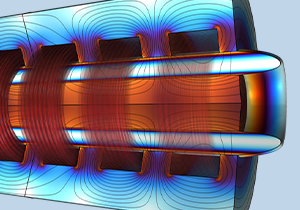
COMSOL® 多物理场仿真在电气绝缘中的应用
Webinar
Dec 05
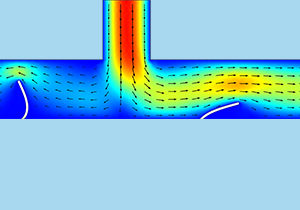
微流体器件的多物理场仿真
Webinar
Nov 30
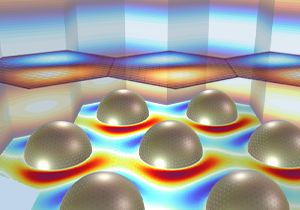
半导体制造中的晶体生长仿真
Webinar
Nov 28
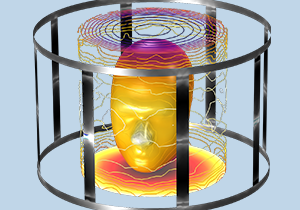
COMSOL® 多物理场仿真在医疗设备研发中的应用
Webinar
Nov 21
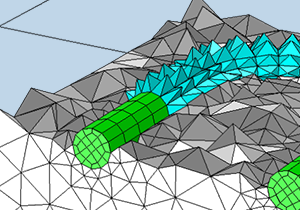
COMSOL® 中的网格划分
Webinar
Nov 16
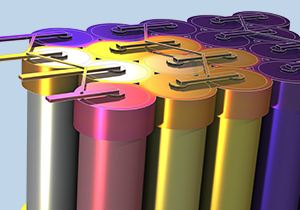
锂离子电池热失控仿真
Webinar
Nov 14
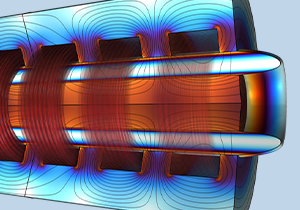
COMSOL® 中的磁流体仿真
Webinar
Nov 09
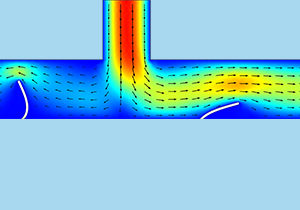
COMSOL® 地下水流及多孔介质流仿真
Webinar
Nov 02
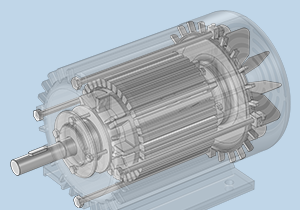
电磁噪声的仿真分析
Webinar
Oct 31
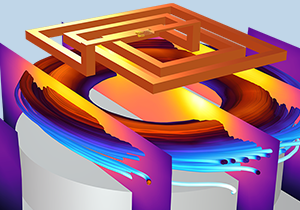
使用 COMSOL Multiphysics® 仿真 PVD/CVD 薄膜沉积工艺
Webinar
Oct 27
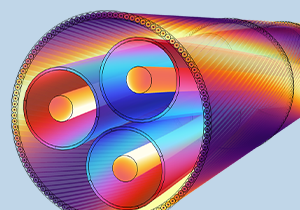
COMSOL® 多物理场仿真优化电缆设计
Webinar
Oct 20
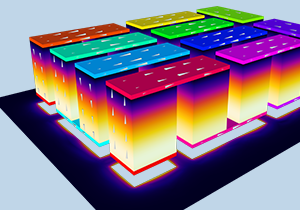
COMSOL® 的求解器简介
Webinar
Oct 13
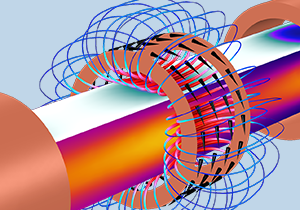
COMSOL® 中的感应加热仿真
Webinar
Sep 26
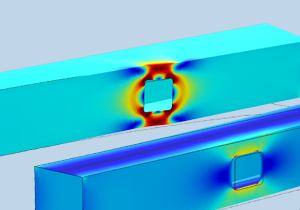
COMSOL® 中的岩土力学仿真
Webinar
Sep 19
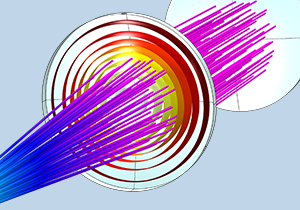
多物理场仿真在激光加工中的应用
Webinar
Sep 15
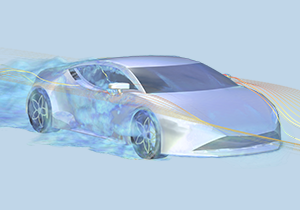
计算流体力学(CFD)多物理场仿真
Webinar
Sep 12
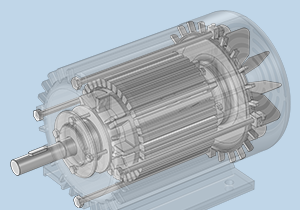
使用 COMSOL® 求解大型模型
Webinar
Sep 08
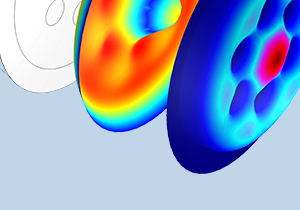
COMSOL® 中的声学超材料仿真
Webinar
Sep 05
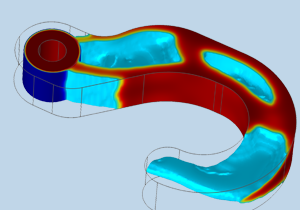
使用 COMSOL Multiphysics® 进行设计优化
Webinar
Sep 01
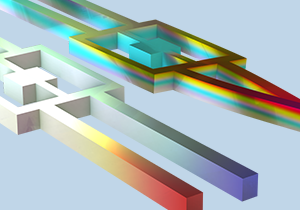
COMSOL® 的压电材料和器件仿真
Webinar
Aug 29
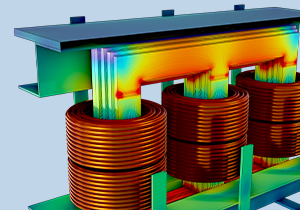
COMSOL® 中的变压器仿真
Webinar
Aug 25
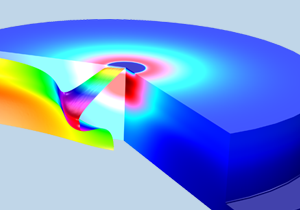
COMSOL® 中的半导体器件仿真
Webinar
Aug 22
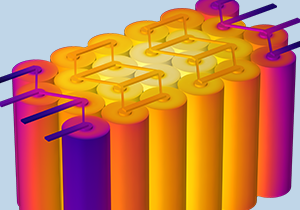
COMSOL® 中的锂电池仿真
Webinar
Aug 18
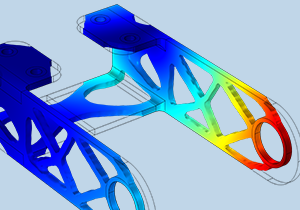
COMSOL® 的结构力学仿真
Webinar
Aug 15
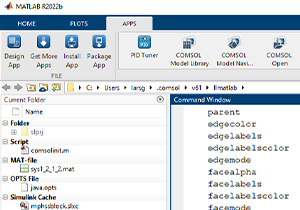
COMSOL® 中的 LiveLink™ for MATLAB® 和 LiveLink™ for Simulink® 功能简介
Webinar
Aug 11
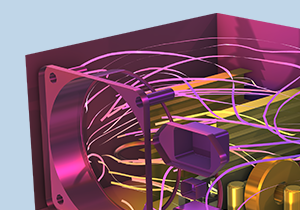
电子设备热管理的仿真分析
Webinar
Aug 04
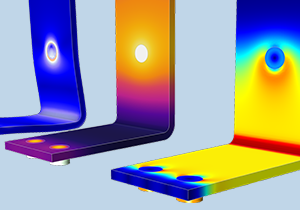
电磁损耗的仿真分析
Webinar
Jul 28
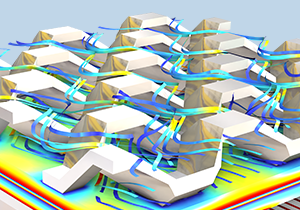
氢燃料电池与水电解槽的多物理场仿真
Webinar
Jul 25
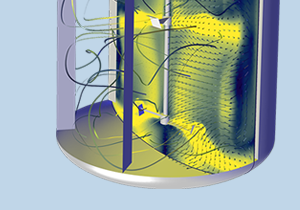
COMSOL® 中的多相流仿真
Webinar
Jul 21
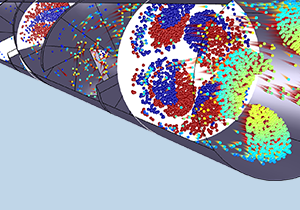
粒子追踪方法的建模仿真
Webinar
Jul 18
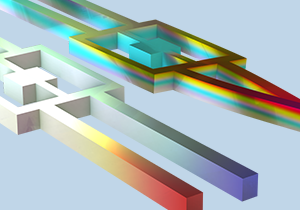
MEMS 器件的多物理场建模和仿真
Webinar
Jul 14
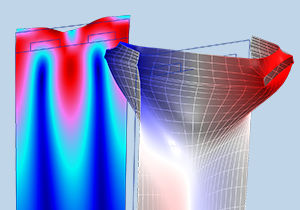
SAW 和 BAW 滤波器的建模仿真
Webinar
Jul 07
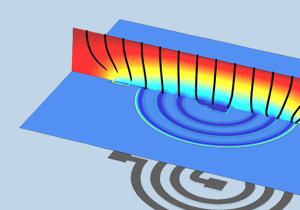
COMSOL® 中的电镀仿真
Webinar
Jul 04
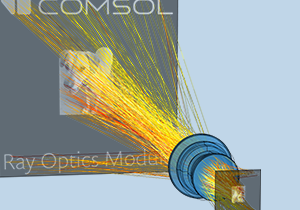
COMSOL® 中的射线光学仿真
Webinar
Jun 30
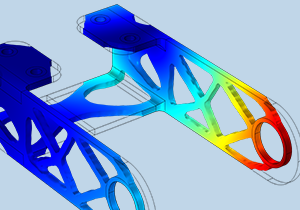
COMSOL® 中的热应力仿真
Webinar
Jun 16
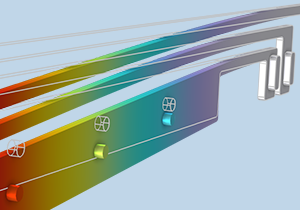
Introdução ao COMSOL Multiphysics® em 18 minutos
Webinar
Jun 13
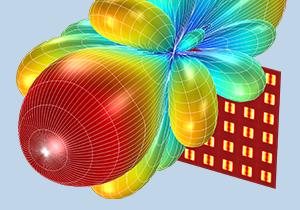
COMSOL® 中的高频电磁场仿真
Webinar
Jun 13
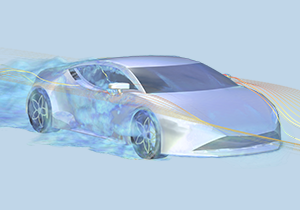
COMSOL® 中的流固耦合仿真
Webinar
Jun 09
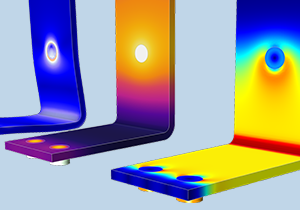
COMSOL® 中的传热仿真
Webinar
Jun 06
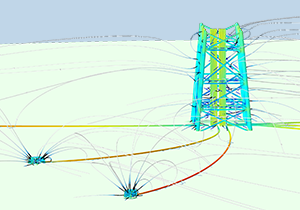
COMSOL® 中的腐蚀与防护仿真
Webinar
Jun 02
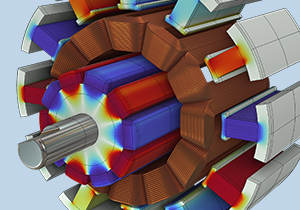
COMSOL® 中的低频电磁场仿真
Webinar
May 23
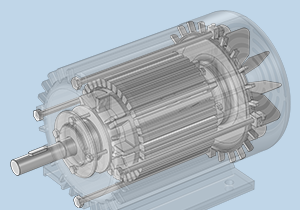
在 COMSOL® 中进行 CAD 导入及几何模型处理
Webinar
May 19
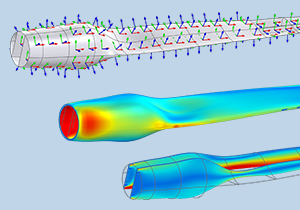
COMSOL® 中的复合材料仿真
Webinar
May 16
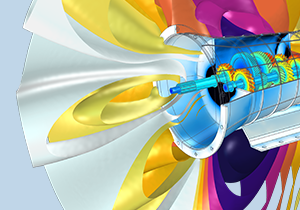
声学与振动的多物理场仿真
Webinar
May 12
Showing 6 of 213 events
Showing 213 of 213 events
Trainings by Certified Consultants
- Product Information
- Products
- Specification Chart
- License Options
- System Requirements
- Release History
- Support and Services
- Support Center
- My Support Cases
- Knowledge Base
- Partners and Consultants
- Documentation
- Product Download
- Company
- About
- Careers
- Press
- Contact Us
- |
- Privacy Policy
- |
- Trademarks
- |
- Cookie Settings
- © 2025 by COMSOL. All rights reserved