Computational Fluid Dynamics (CFD) Blog Posts
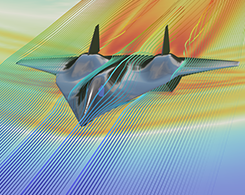
Modeling the Speed and Stealth of the Darkstar
What would the shock waves around the Darkstar really look like at Mach 7.5? How stealthy is this hypersonic jet? Here, we use modeling and simulation to find out.
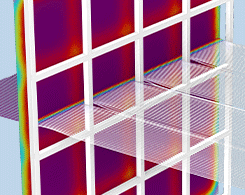
Examining an Air Filter with a RANS Turbulence Model
Modeling and simulation can be used to analyze and better understand turbulent flow in a variety of systems. See one example here.
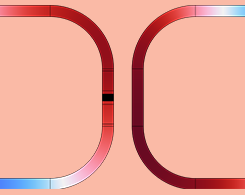
Modeling Acoustic Energy Generation in Thermoacoustic Engines
Thermoacoustic engines do not use moving parts, keeping their structure very simple. Learn more about these engines and how to model them here.
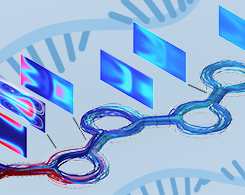
Using Simulation to Guide mRNA Vaccine Production
In recent times, lipid nanoparticles have gained public attention for their use in mRNA vaccine production. Read how Veryst Engineering is using simulation to help guide this process.

Validating Transonic Flow Results with the ONERA-M6 Wing Model
When using simulation software, your models’ results should accurately reflect the real-world phenomena you are simulating. 1 way to check this is by using a validation model.
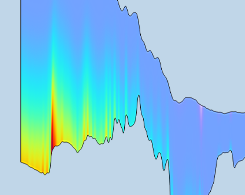
Investigating Glacier Motion with Viscoelastic Ice Simulations
Researchers at the Alfred Wegener Institute (AWI) use viscoelastic ice simulations to study the occurrence of crevasses in glaciers and iceberg calving. Learn how here.
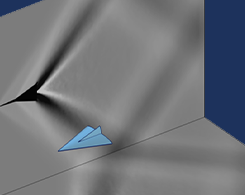
Creating Schlieren-Type Visualizations in COMSOL Multiphysics®
Did you know that Schlieren imaging might predate written history? Here, we explore this ancient imaging technique with CFD modeling.

Pasta alla Simulazione: Modeling an Extruder in COMSOL®
On an industrial scale, extruders mix and knead raw pasta dough. Avoid issues with looks, taste, and safety by modeling the extrusion process.