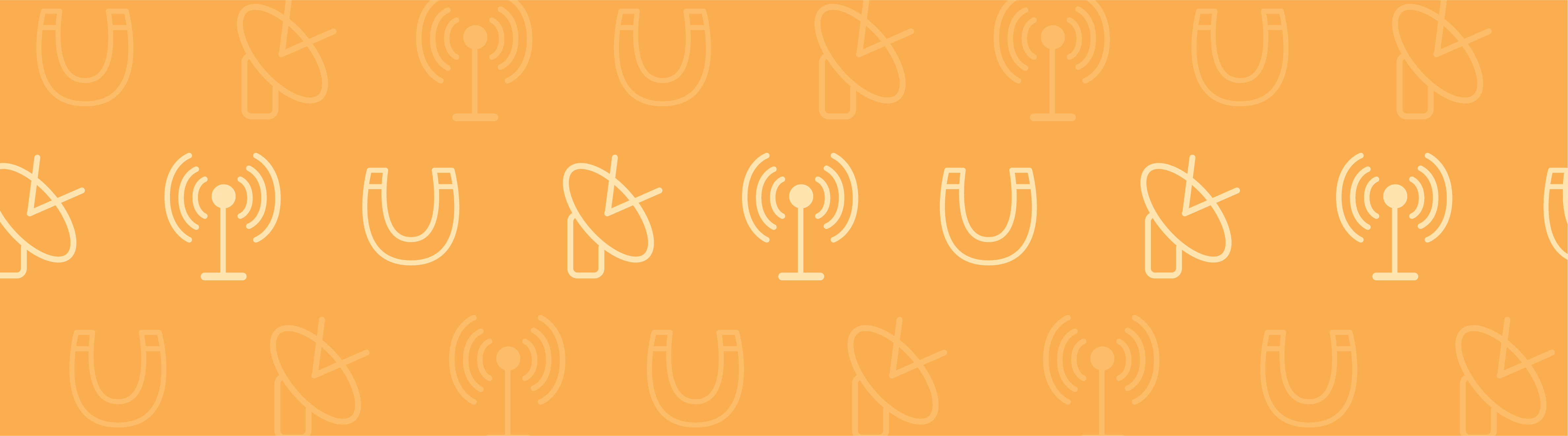
Over the years, energy harvesting has become a popular approach to power small wireless devices. For energy harvesters to yield optimal results, it is important that their design configurations maximize the level of power transfer. Here, we will explore the role of simulation in advancing the design of a piezoelectric energy harvester.
Advancing the Power of Wireless Sensor Networks with Energy Harvesting
Wireless sensor networks are used today in a variety of low-power applications, from wearable healthcare to water quality monitoring. These networks include a series of sensors that measure and record physical conditions — often intermittently, over a period of time — at various locations. Through a wireless link, each sensor communicates the information it obtains to other sensors in the network as well as a base location that records the readings from all of the sensors.
One of the biggest challenges in developing wireless sensor networks is balancing energy consumption with efficiency. Battery life in sensors is often limited, making these devices more expensive to deploy, while reducing their number of applications. That’s where energy harvesting comes into play. In this process, energy is gathered from an external source (e.g., solar or thermal power) and converted into usable energy. Energy harvesting is beneficial, as it makes use of energy that would have otherwise been lost, helping to optimize the power of devices while extending their operational lifetime.
As previously referenced, energy can be harvested from the environment in a number of ways. One example is when mechanical strain is converted into electrical energy, also known as piezoelectric energy harvesting. A potential source of mechanical strain is local variations in acceleration. This is the case when a wireless sensor is mounted on a piece of machinery that is vibrating.
Let’s analyze such an energy harvester configuration in COMSOL Multiphysics.
Using Simulation to Analyze a Piezoelectric Energy Harvester
The Piezoelectric Energy Harvester tutorial model is designed to represent a simple “seismic” energy harvester. The device features a piezoelectric biomorph clamped at one end of the vibrating machinery and a proof mass mounted on the other end. A ground electrode is embedded within the biomorph, with two electrodes on the cantilever beam’s exterior surfaces. This design scheme ensures that an equal voltage is induced on the exterior electrodes.
Geometry of a piezoelectric energy harvester.
Our series of simulation analyses begins with addressing the power output as a function of vibration frequency. The plot below shows the input mechanical power and the power harvested, along with the voltage that is induced across the piezoelectric biomorph when acceleration occurs. In this case, the fixed electrical load is 12 kΩ and the acceleration magnitude is 1 g. From the results, we can identify a peak voltage at 76 Hz. This calculation is close to the resonant frequency computed for the cantilever in a separate eigenfrequency analysis (73 Hz).
Power output as a function of vibration frequency.
Let’s now measure the power output as a function of the electrical load resistance. In this scenario, we apply an acceleration of 1 g vibrating at 75.5 Hz. The results, shown in the following graph, indicate that the peak of power harvested correlates to an electrical load of 6 kΩ.
Power output as a function of electrical load resistance.
Lastly, we analyze the voltage and mechanical/electrical power as a function of mechanical acceleration. Here, the acceleration is set at 75.5 Hz, with a load impedance of 12 kΩ. As the plot below illustrates, there is a linear relationship between the voltage and the load, while the harvested energy increases quadratically.
Power output as a function of acceleration.
These results show good qualitative agreement when compared with experimental findings.
Concluding Thoughts
Simulation offers a simplified approach to studying and optimizing energy harvesting devices. The ability to easily test different device configurations accelerates the design process, while helping to produce more efficient energy harvesters. As the efficiency of these devices continues to grow, a greater number of technologies will have the chance to benefit from energy harvesting.
Next Steps
- Download the tutorial model: Piezoelectric Energy Harvester
- Read a related user story: Modeling Optimizes a Piezoelectric Energy Harvester Used in Car Tires
Comments (11)
Toyabur Rahman
July 6, 2016what the difference will be in modeling if I want to simulate PZT cantilever based 3D energy harvester like 2D application given in this application gallery ?
Toyabur Rahman
July 6, 2016what the difference will be in modeling if I want to simulate PZT cantilever based 3D energy harvester like 2D application given in application gallery ?
Bridget Cunningham
July 11, 2016 COMSOL EmployeeHi Toyabur,
Thank you for your comment.
For questions related to your modeling, please contact our support team.
Online support center: https://www.comsol.com/support
Email: support@comsol.com
Best,
Bridget
Thien
October 10, 2017Hi Bridget Cunningham,
Thank you for your nice topic. I am wondering how do you calculate the mechanical power as input of the PEH. Could you please explain a little bit about your calculus?
Thanks in advance,
Thien
Chien Liu
October 13, 2017 COMSOL EmployeeDear Thien,
Thank you for the comments. The mechanical power is computed by cycle averaging the product of the body force and the velocity fields. You can download the model and the PDF documentation from the link above (under the section titled “Next Steps”).
Sincerely,
Chien
Pradeesh EL
October 20, 2017Mine research work i similar to this one. But i have used 3D model and point load.
In this model,
1.There is an Acceleration Dependency study mode, under this Auxiliary Sweep is used with range of 0.25 to 2. Does this is an amplitude of an particular frequency?
2. Did you have calculated the gravity of mass proof or Beam. [In the parameter you have added the (g) that’s why i am asking.]
3. You have used some expressions for ploting of Global Data, Is there any way to express the expressions without equations.
4. You have choose top and bottom of PZT as an Terminal and Ground, Why we can’t choose the sides of PZT as an terminal and Ground.
Thank you,
Pradeesh .E.L
Caty Fairclough
November 6, 2017Hi Pradeesh,
Thanks for your comment.
For questions related to your modeling, please contact our Support team.
Online Support Center: https://www.comsol.com/support
Email: support@comsol.com
Bdhaifi Elmuzzammel
February 6, 2018Hi,
I have something like your application, but I don’t know how to plot the output power , can you help me ?
thank you.
亚军 曹
March 2, 2019Hi
I did this case recently, there are some questions about that, for example, in this case, the connection is in parallel, so what should i do if i want to connect with serial ? thanks you!
Brianne Christopher
March 11, 2019 COMSOL EmployeeHello,
Please contact our Support team for questions related to your modeling:
Online Support Center: https://www.comsol.com/support
Email: support@comsol.com
PINKI SHRIVAS
May 15, 2020As in this MEMS piezoelectric energy harvester module they have used formula valuation for voltage ,electrical power and mechanical power graphically .Can we calculate electrical power for trapezoidal bimorph using same formula .Please help me to calculate electrical power graphically for my 3D STRUCTURE.