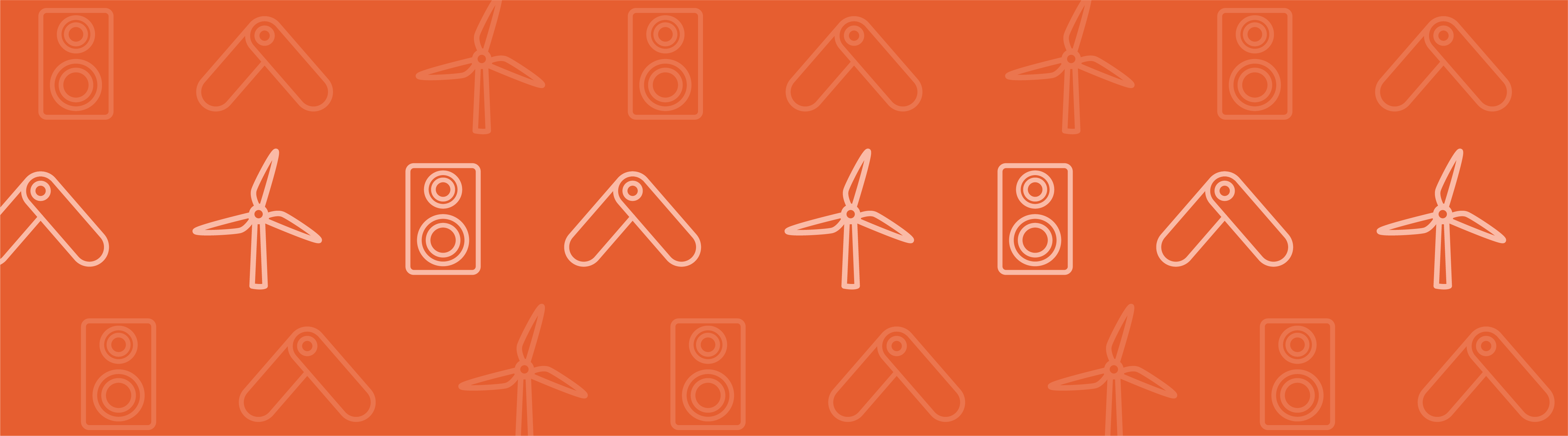
With all of the other components of an automobile to consider, it is easy for drivers to forget to routinely check tire pressure. Thankfully, companies are actually beginning to assemble most of their newer vehicles with built-in tire pressure monitoring sensors. These devices are placed at the bottom of the tire hub and measure air pressure automatically — all while the car is still in motion.
Tire Shape Is Indispensable to Driving Performance
Keeping that perfectly round tire shape is important for more than just aesthetics. The lower the air pressure in a tire gets, the harder it is for the car to move forward. Every tiny leak is a source of strain for the vehicle, which can be fixed — as long as the driver is aware of the low pressure in the first place.
Tire pressure monitoring sensors, designed by Schrader Electronics, are meant to mount directly on the wheel assembly and when measurement gets below a certain pressure, a warning goes off.
I was lucky enough to speak with the researchers who work on the Schrader sensor models (their company actually builds 45 million every year). If you find yourself in a fairly new vehicle, chances are it contains a pressure sensor from Schrader. Designing these sensors for functionality and longevity is a huge part of keeping cars effective and safe.
Centrifugal Loading Caused by Wheel Rotation
The Schrader research team, led by Christabel Evans, tested out different shapes and components so that the sensors would last and still be able to relay measurement information back to the automobile’s dashboard without external interference. They relied on COMSOL Multiphysics together with the Structural Mechanics Module and CAD Import Module to help them choose the right parameters.
The geometry of their model consists of a circuit transmitter in a solid enclosure. The enclosure takes the brunt of the force and pressure while the wheel spins. For this reason, Schrader needed to model everything the sensor might encounter on the road, including tire fitment, vibration, and shock. They also had to factor in all of the important natural parameters, such as pressure and crush load, centrifugal force, and temperature change.
Schrader’s tire pressure sensor fits directly into the rim of the wheel assembly. Image courtesy of Adam Wright, Schrader Electronics.
A model showing the enclosure illustrates that different applied forces can cause deformation in the device over time. By using finite element analysis (FEA) and simulation throughout the process of product design and testing, Schrader was able to isolate or couple variables as needed, allowing them to work towards the best design. This gave them the flexibility to build and refine as they went.
10x amplification of stress and deformation on the transmitter housing as a result of centrifugal loading, which is produced by the wheel’s rotation.
A Spin Test to Highlight Bolt Stress Points
As they narrowed down the best design, Schrader also simulated the equipment used for testing the device rotating on the tire. They mapped where the greatest stress occurred and found that it mostly took place along the bolts of the collar. This allowed them to make all of the necessary adjustments to reinforce those areas and continue to optimize the design as they worked.
The spin test works at a very high speed, simulating conditions the sensors are exposed to. The model shows an increase in stress along all of the sections of the model where bolts are located.
Spinning Several Wheels at Once
Perhaps the most useful feature in COMSOL Multiphysics (for the Schrader engineers) was the ability to test various parameters, shapes, and designs. It was much easier to get the most out of their computational power by running several models simultaneously. As they continue their research, they plan to keep focusing on failure analysis to fortify their design and continue to improve their product’s accuracy and life span.
Further Reading
- Learn more about how Schrader used simulation to drive their product design by reading the full-length story “Optimizing Built-in Tire Pressure Monitoring Sensors” in COMSOL News 2014.
Comments (0)